Cemento, Calce e Cartiere
La nostra offerta per l’industria del cemento, della calce e della carta
Il processo di calcinazione dei carbonati di calcio e il loro successivo trattamento termico svolgono un ruolo fondamentale in numerosi settori, in particolare nell’edilizia e nell’industria chimica.
Il clinker di cemento e la calce viva sono componenti essenziali nei materiali da costruzione. La calce viva è inoltre ampiamente utilizzata in diversi processi industriali, come la produzione della polpa di cellulosa, della soda ela raffinazione dello zucchero. Attualmente, la produzione basata su questi processi è sottopostai a forti pressioni per massimizzare l’efficienza ed essere conforme ai requisiti di sostenibilità. Le emissioni di CO₂ derivanti dalle materie prime hanno un impatto significativo sull’economia della calcinazione, pertanto è essenziale ottimizzare ogni fase del processo. LE eampagne produttive prive di guasti, e con brevi soste per la manutenzione e rivestimenti refrattari del forno ad alta efficienza termica possono offrire un vantaggio competitivo significativo. La missione di PCO è di offrire soluzioni ai propri partner nel campo delle tecnologie refrattarie per forni da calce e da cemento – dagli studi ingegneristici e la selezione congiunta delle soluzioni dei materiali e dei metodi di installazione adeguati, fino alla logistica globale, al montaggio e alla supervisione. Crediamo che l’affidabilità dei nostri prodotti e servizi, combinata con un’assistenza completa, permetta di ridurre al minimo le interruzioni produttive e aiuti i nostri clienti a migliorare la loro competitività e raggiungere gli obiettivi di sostenibilità.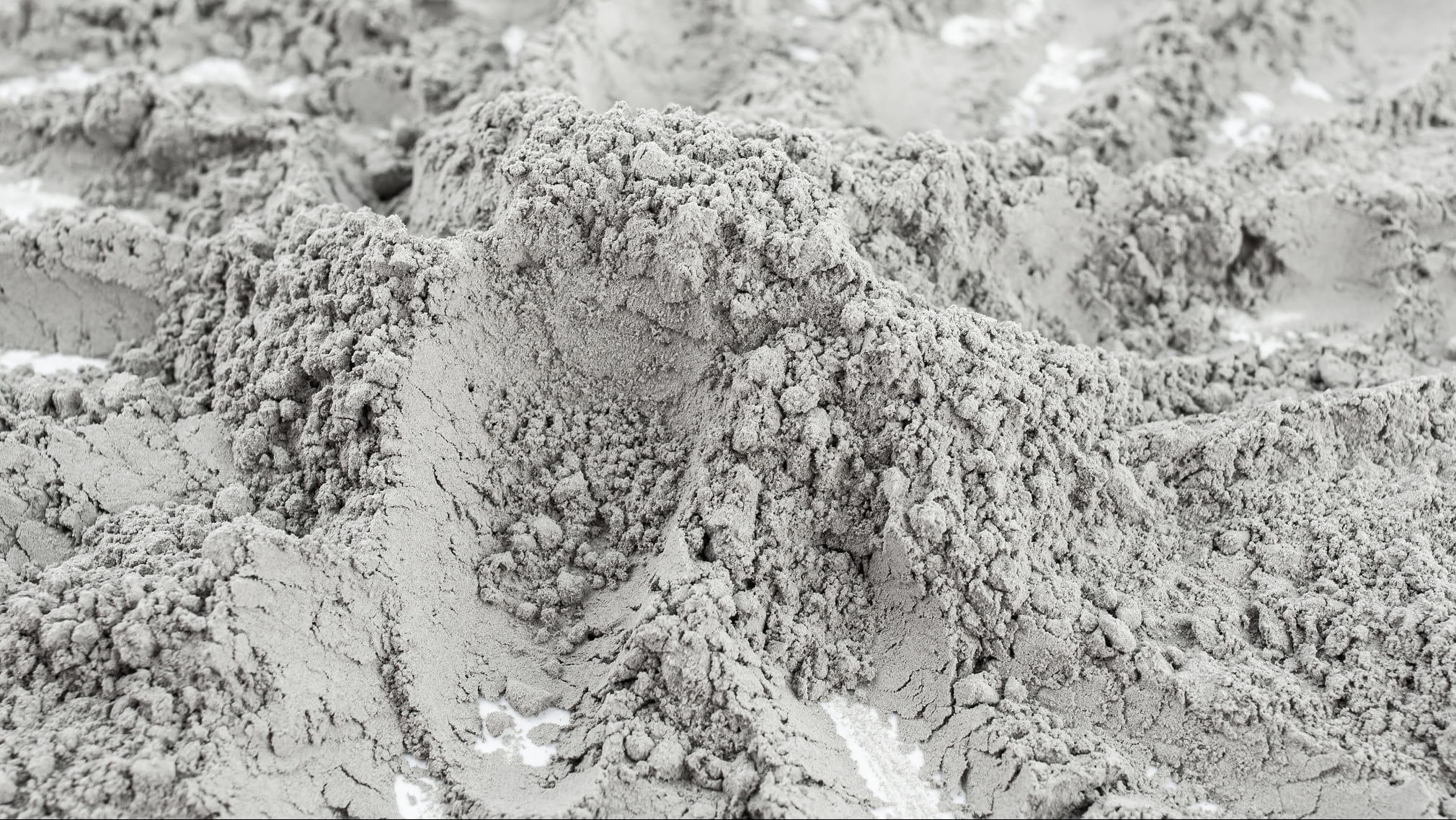
In cosa possiamo aiutare?
Progettiamo
- La selezione delle qualità di materiali refrattari più ideonei, in base alle condizioni operative del processo produttivo
- La configurazione ottimale del rivestimento refrattario, tenendo conto della struttura dell’impianto, delle zone del processo, delle condizioni operative e delle preferenze dell’utilizzatore
- Analisi dei flussi termici per le diverse proposte di rivestimento (confronti A/B)
- Ottimizzazione della progettazione del rivestimento per prolungarne la durata e ridurre le perdite di calore
Produciamo e forniamo
- Prodotti a base di chamotte e ad alto tenore di allumina con elevata resistenza all’abrasione, destinati al rivestimento di torri di raffreddamento, condotti d’aria terziaria, calcinatori, camere di risalita negli impianti cementieri, nonché alle zone di ingresso e uscita dei forni da calce
- Calcestruzzi innovativi a basso contenuto o privi di cemento, arricchiti con SiC e ZrO₂, idenei per una vastia gamma di applicazioni nei cementificigli
- Prodotti isolanti per strati di protezione nei forni verticali e rotativi, comprese qualità con elevata resistenza meccanica
- Prodotti prefabbricati pronti per l’installazione, che non necessitano pre-riscaldo in cantiere
Installiamo
- Smontaggio e installazione del rivestimento refrattario in tutte gli impianti dei cementifici, così come nei forni a singolo e doppio tino
- Rimozione e raccolta del rivestimento refrattario
- Riparazioni ordinarie e interventi di emergenza durante le campagne di manutenzione
- Consulenza tecnica – analisi delle cause di usura, ottimizzazione della durata del rivestimento e supervisione del montaggio dei refrattari
Fours et autres applications à haute température
Cicloni stadi superiori
Gli stadi superiori dei cicloni svolgono un ruolo essenziale nella produzione del clinker, garantendo il corretto mescolamento, trasferimento e distribuzione delle materie prime. In questa zona, il materiale viene riscaldato gradualmente e le temperature possono raggiungere i 600 °C. Il processo è continuo e richiede materiali refrattari durevoli e resistenti all’usura. Il rivestimento del ciclone si divide in tre aree principali: la volta, il cilindro e il cono. La sfida maggiore per il rivestimento refrattario in questa parte dell’impianto è l’abrasione provocata dal flusso intenso delle materie prime, mentre l’effetto della temperatura elevata è relativamente secondario. Poiché gli stadi superiori hanno un ciclo di vita decennale o pluridecennale, durante il quale sono soggetti a molteplici periodi di manutenzione, è fondamentale impiegare materiali particolarmente resistenti. PCO propone soluzioni refrattarie specifiche per le condizioni operative dei cicloni superiori. In condizioni standard si utilizzano mattonia a base di chamotte della gamma NORMATON, mentre in presenza di abrasione intensa si consigliano l’uso di mattoni refrattari extra resistenti della gamma EXTRATON. In alcuni casi, si dimostrano efficaci anche i rivestimenti in calcestruzzo, che garantiscono un'ulteriore durata e stabilità del funzionamento del ciclone.
Ambito: Progettazione del rivestimento Fornitura dei materiali refrattari Montaggio del rivestimento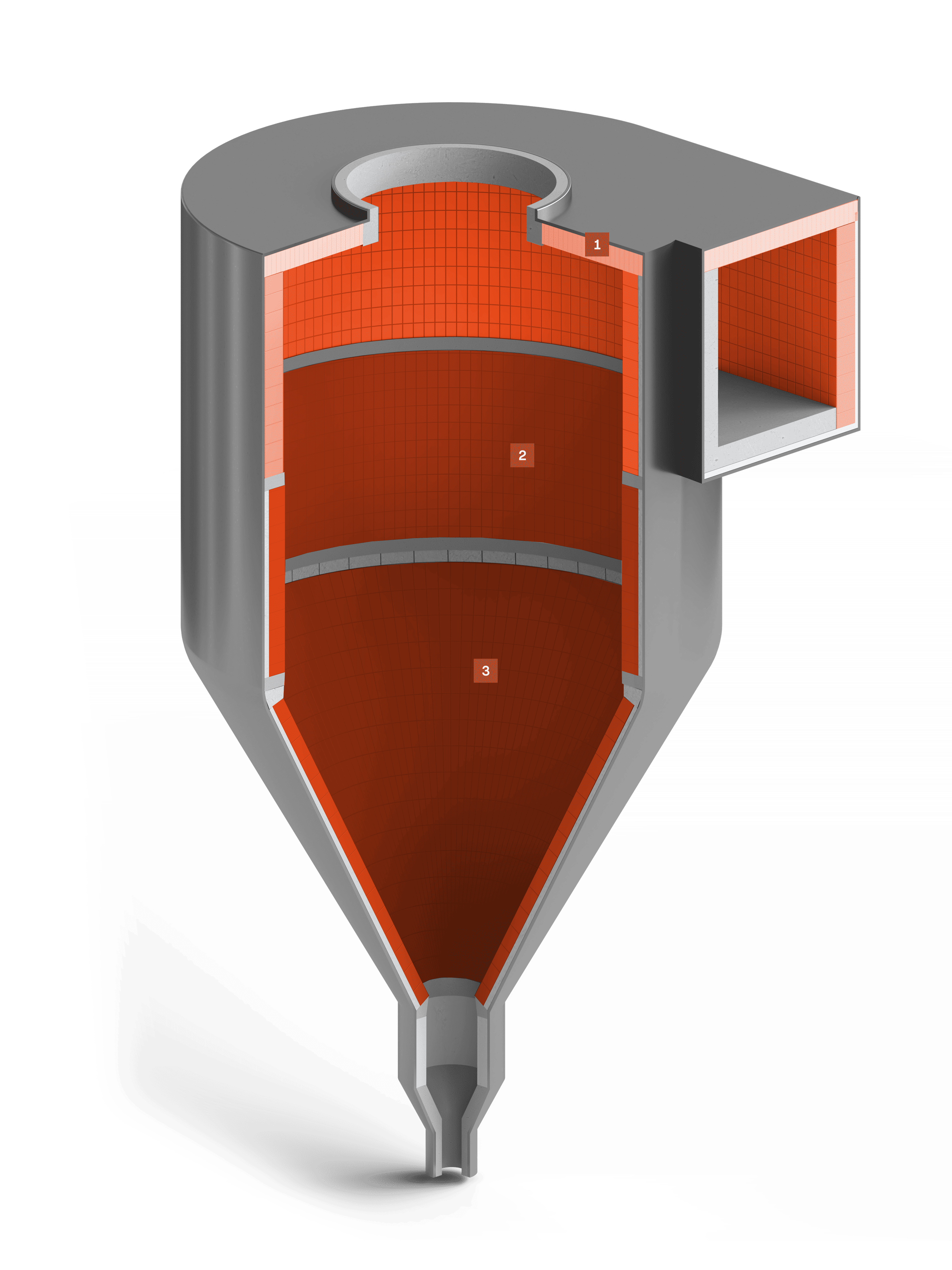
La volta del ciclone superiore è principalmente esposta all'abrasione gassosa, causata dall'azione delle particelle volatili della carica. In questa zona, l’influenza della temperatura e delle sollecitazioni meccaniche è minimia, il che si traduce in condizioni operative relativamente lievi. Il rivestimento della volta è composto da più strati sovrapposti, nei quali i mattoni a cuneo svolgono un ruolo essenziale sia nello strato di lavoro sia in quello isolante. La struttura multistrato assicura una protezione adeguata contro i gas aggressivi e riduce l’usura del materiale refrattario. Data la moderata severità delle condizioni operative, in questa zona sono particolarmente adatti i prodotti a basso contenuto di allumina della serie EXTRATON, nonché i mattoni isolanti leggeri ISOLUX. Questi materiali garantiscono una resistenza sufficiente all’abrasione gassosa, mantenendo al tempo stesso ottime proprietà isolanti.
Il cilindro del ciclone superiore è esposto a sollecitazioni di tipo abrasivo e meccanico, sebbene di entità moderata. Le sollecitazioni meccaniche non sono elevate, il che consente l’impiego di soluzioni refrattarie standard. Il rivestimento del cilindro è costruito analogamente a quello della volta e si compone di più strati, con un uso predominante di mattoni a cuneo sia nella parte di lavoro sia in quella isolante. Questa costruzione garantisce una distribuzione uniforme dei carichi e una protezione duratura contro l’usura. In presenza di condizioni operative moderate, per questa zona si impiegano gli stessi materiali della volta – EXTRATON a basso contenuto di allumina e mattoni isolanti ISOLUX – ottenendo così un buon equilibrio tra resistenza all’abrasione e isolamento termico.
Il cono rappresenta la parte del ciclone soggetta a maggiori sollecitazioni meccaniche, anche se nel complesso il rischio per il rivestimento refrattario resta contenuto. Ciò è dovuto alla geometria particolare di questa zona, che influenza l’intensità delle sollecitazioni meccaniche. Per adattarsi meglio alla geometria complessa del cono e facilitarne la posa, il rivestimento è realizzato in calcestruzzo refrattario. Questo tipo di costruzione consente una distribuzione uniforme del materiale sulle superfici irregolari, garantendo resistenza e stabilità.
Come possiamo aiutarti
Se desideri ricevere una consulenza gratuita o porre una domanda sulla scelta del rivestimento refrattario, lasciaci i tuoi dati – ti richiameremo!
ContattaciCome minimizzare lo sfaldamento della superficie dei mattoni refrattari durante cicli termici rapidi?
Quale calcestruzzo da riparazione offre la migliore resistenza all’abrasione provocata da particelle volatili?
Come proteggere il rivestimento ceramico dalla corrosione alcalina e dagli attacchi salini?
Cicloni stadi inferiori
Gli stadi inferiori dei cicloni svolgono un ruolo chiave nel processo di produzione del clinker, garantendo un’intensa miscelazione, trasferimento e distribuzione delle componenti delle materie prime. In questa zona le temperature possono raggiungere i 950 °C, superando quindi quelle tipiche dei cicloni superiori. Un aspetto fondamentale del funzionamento dei cicloni inferiori è la parziale precalcinazione della pietra calcarea, che contribuisce ad aumentare l’efficienza delle fasi successive del processo. Dal punto di vista del rivestimento refrattario, gli stadi inferiori si suddividono in volta, cilindro e cono inferiore. In questa parte dell’impianto, il rivestimento è esposto a condizioni molto più aggressive rispetto a quelle presenti nei cicloni superiori. In condizioni operative standard, si impiegano mattoni a base di chamotte arricchiti con andalusite e carburo di silicio, appartenenti alle linee EXTRATON e ABRAL, che offrono un’elevata resistenza all’abrasione e agli attacchi alcalini. Nei casi in cui si utilizzano rivestimenti in calcestruzzo, sono raccomandati i materiali GELCAST, MULCAST e NxGel, che mostrano un'alta resistenza all'azione di combustibili alternativi e ad ambienti chimicamente aggressivi
Ambito: Progettazione del rivestimento Fornitura dei materiali refrattari Montaggio del rivestimento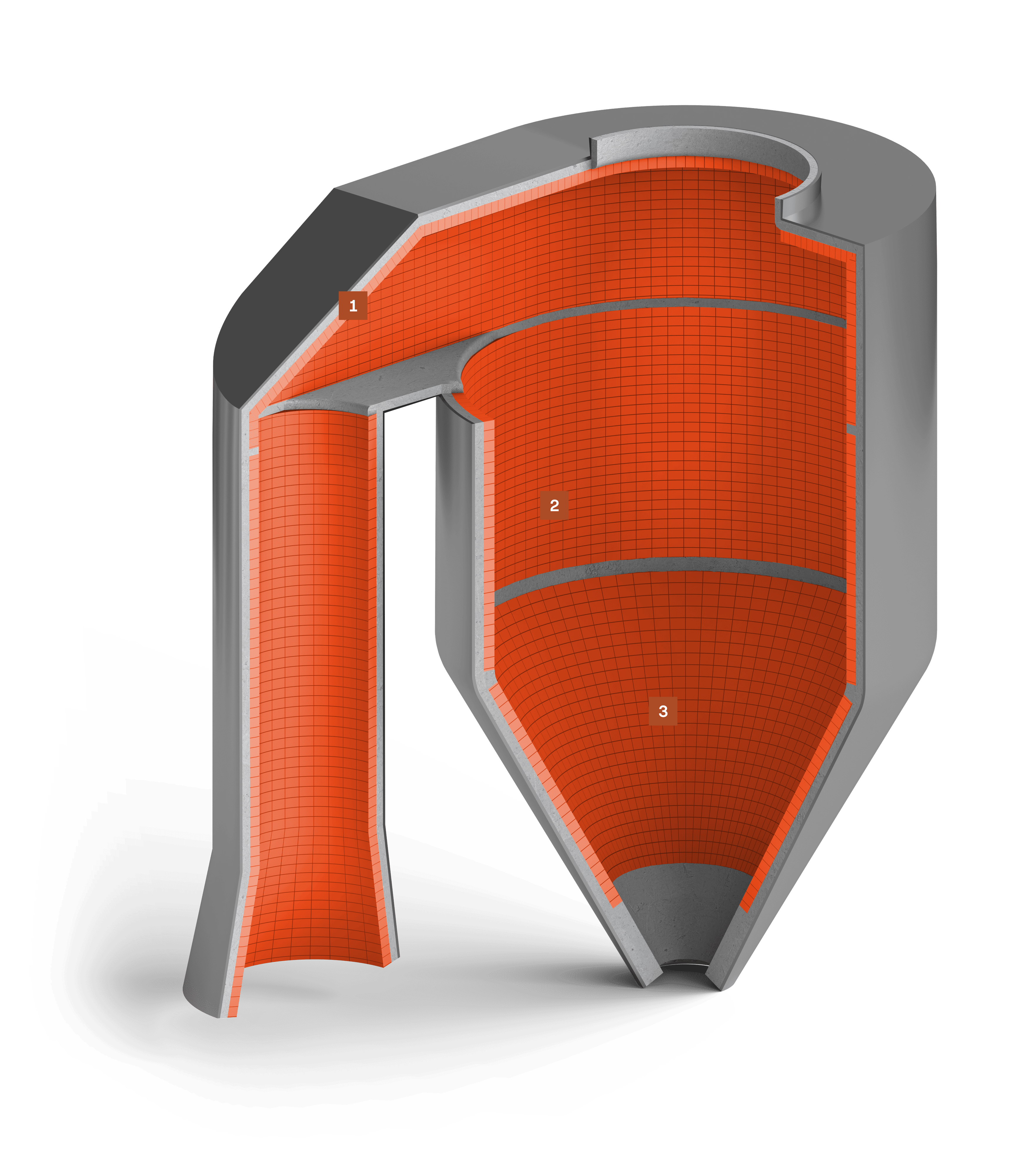
La volta del ciclone inferiore è principalmente esposta all’abrasione da parte dei gas carichi di particelle volatili. Sebbene le sollecitazioni meccaniche e termiche siano relativamente contenute, le condizioni operative risultano più impegnative rispetto a quelle tipiche dei cicloni superiori. Inoltre, il rivestimento deve resistere ad attacchi chimici e alla formazione di incrostazioni, fenomeni che aumentano il rischio di degrado. La volta è costruita con una struttura multistrato composta da diversi livelli sovrapposti, nei quali i mattoni a cuneo svolgono un ruolo centrale sia nello strato di lavoro sia in quello isolante. Questa configurazione permette una distribuzione graduale dei carichi e una maggiore protezione contro l’abrasione abrasiva e l’aggressione chimica.
Il cilindro del degli stadi inferiori dei cicloni è soggetto a una combinazione di sollecitazioni: abrasione, usura meccanica e attacco chimico aggressivo, compresa la corrosione alcalina. Tali carichi multidirezionali richiedono che il rivestimento sia resistente sia all’erosione meccanica intensa sia alla degradazione chimica, rendendo le condizioni operative in questa zona particolarmente difficili. Come per la volta, il rivestimento del cilindro è costituito da più strati, in cui prevalgono i mattoni a cuneo utilizzati sia nella parte di lavoro sia in quella isolante. La struttura multistrato consente di distribuire uniformemente le sollecitazioni e prolungare la durata del rivestimento.
Il cono degli stadi inferiori dei cicloni è la zona più sollecitata da forze meccaniche, chimiche e abrasive. A causa della geometria irregolare del cono e della complessità del processo di posa, il rivestimento in questa zona viene realizzato con calcestruzzo refrattario. Questa soluzione permette di adattare con precisione il materiale alla forma complessa del cono, minimizzando il rischio di tensioni localizzate e danni strutturali. In questa zona è fondamentale che il rivestimento sia altamente resistente alle sollecitazioni di tipo meccanico, chimico e abrasivo.
Come possiamo aiutarti
Se desideri ricevere una consulenza gratuita o porre una domanda sulla scelta del rivestimento refrattario, lasciaci i tuoi dati – ti richiameremo!
ContattaciQuale calcestruzzo refrattario offre il miglior equilibrio tra resistenza all’abrasione e tolleranza allo shock termico
Come compensare la differente dilatazione tra gli strati refrattari e l’involucro in acciaio per evitare fessurazioni?
Come ridurre la formazione di incrostazioni da polvere sul rivestimento refrattario?
Calcinatore
Il calcinatore, utilizzato principalmente per il preriscaldamento e la calcinazione delle materie prime calcaree, trasferisce parte del processo di combustione e decarbonizzazione dal forno rotativo alla torre di scambio termico. Grazie all’utilizzo di combustibili alternativi, il calcinatore consente di ridurre le emissioni gassose e i costi operativi. Tuttavia, le condizioni di esercizio sono decisamente più severe, richiedendo l’utilizzo materiali refrattari avanzati. Le temperature operative vanno da 800 °C a 1100 °C, e il canale del calcinatore è esposto non solo a calore elevato, ma anche ad agenti corrosivi come ossidi di zolfo (SOₓ), ossidi di azoto (NOₓ), alcalini, cloro e zolfo, che causano un’importante usura abrasiva del rivestimento. Per questo motivo, si impiegano calcestruzzi refrattari a basso contenuto o privi di cemento, arricchiti con zirconio e carburo di silicio; per le riparazioni si utilizzano anche calcestruzzi a spruzzo.. Nel caso di rivestimenti in mattoni, si raccomandano prodotti ad alto tenore di allumina, resistenti agli attacchi chimici, alle alte temperature e allo shock termico. Il rivestimento del calcinatore è composto da più strati: uno strato di lavoro, uno di protezione e uno isolante, per garantire la sua durata anche in condizioni operative estreme. Il ciclo di manutenzione è di alcuni anni, a seconda in base delle condizioni operative e alla percentuale di combustibili alternativi utilizzati.
Ambito: Progettazione del rivestimento Fornitura dei materiali refrattari Montaggio del rivestimento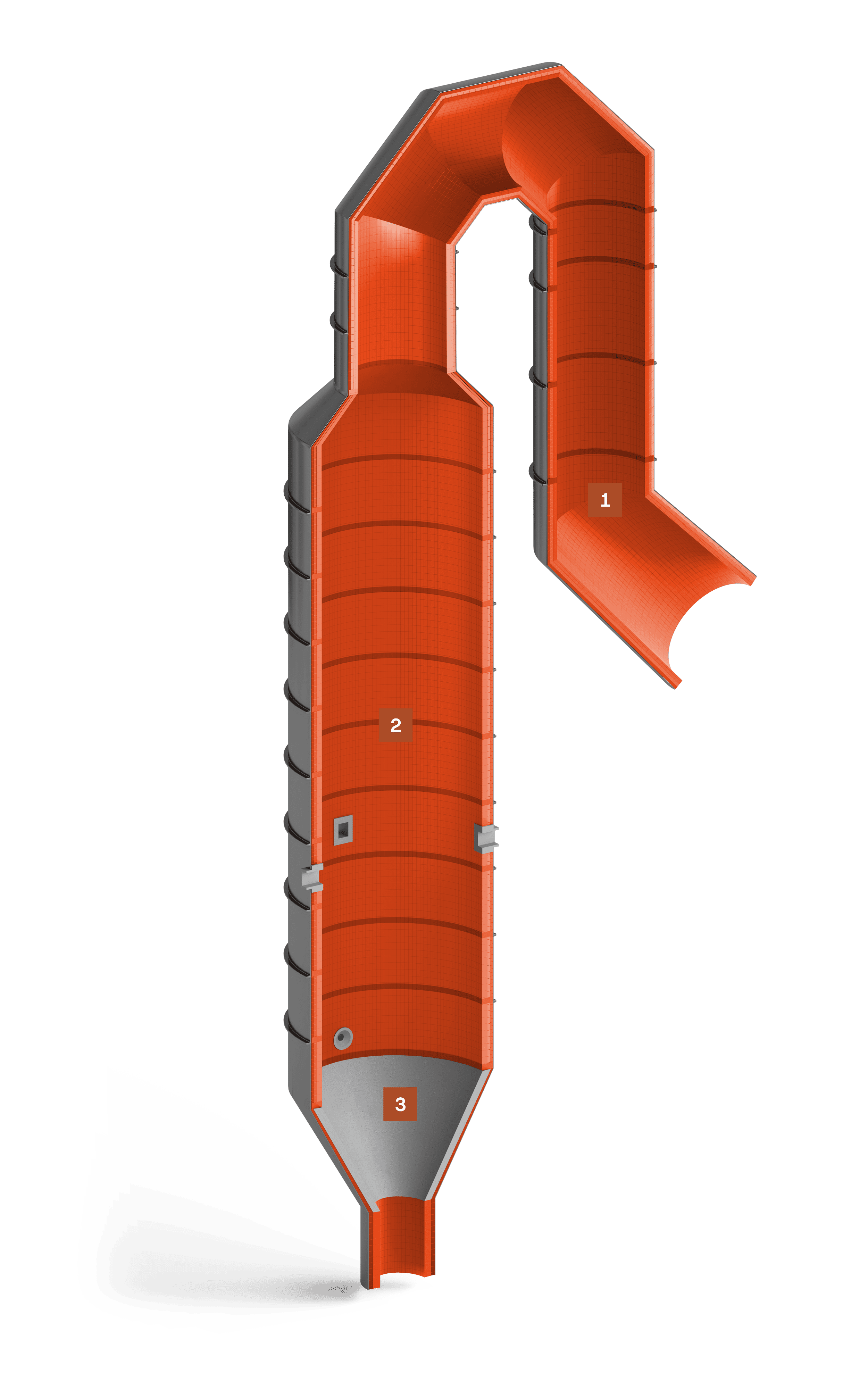
In questa zona le temperature variano tra 700 °C e 900 °C. I principali fattori di rischio per il rivestimento refrattario sono l’abrasione meccanica e l’erosione chimica, dovute all’ingresso della farina cruda. Talvolta si osservano formazioni di incrostazioni sul rivestimento, in particolare derivanti da zolfo e cloro (nei casi di utilizzo di combustibili alternativi). Sono preferibili rivestimenti in calcestruzzo refrattario ad alto tenore di allumina con aggiunta di ZrO₂ o SiC. Se il rivestimento è realizzato con in mattoni, è necessario scegliere qualità ad alto tenore di allumina con buona resistenza all’abrasione e allo shock termico.
In questa zona le temperature superano i 1000 °C e possono raggiungere localmente i 1200 °C nella zona dei bruciatori. È una delle aree più critiche per il funzionamento dei refrattari all’interno dell’intero cementificio. Ciò è dovuto all’utilizzo prevalente di combustibili alternativi, che provocano forti attacchi alcalini. I materiali refrattari – siano essi calcestruzzi o mattoni – devono essere ad alto tenore di allumina, arricchiti con additivi che migliorano la resistenza agli agenti chimici e all’abrasione.
In questa zona le temperature si mantengono elevate, attorno ai 1000 °C. Il rischio principale è rappresentato dagli alcalini che si formano a seguito della combustione del processo di calcinazione. Si utilizzano calcestruzzi ad alto tenore di allumina, a basso contenuto o privi di cemento. Per i rivestimenti in mattoni si raccomandano qualità ad alto tenore di allumina con aggiunta di carburo di silicio. Il rivestimento si incrosta spesso di depositi chimici, sottoprodotto dell’uso di combustibili alternativi; tali incrostazioni devono essere rimosse con aria compressa o acqua durante la manutenzione. Il rivestimento deve inoltre resistere agli impatti meccanici, per resistere alle incrostazioni che si staccano dalle zone superiori del forno.
Come possiamo aiutarti
Se desideri ricevere una consulenza gratuita o porre una domanda sulla scelta del rivestimento refrattario, lasciaci i tuoi dati – ti richiameremo!
ContattaciQuale calcestruzzo a spruzzo che resiste meglio all’abrasione del clinker sinterizzato e alla corrosione da CO₂?
Quale tipo di materiale refrattario è più adatto per cicli di esercizio brevi e con elevato rischio di shock termico?
Come progettare il rivestimento e la posizione del bruciatore per evitare surriscaldamenti localizzati sul mantello?
Condotto d’aria terziaria (TAD)
Nel condotto d’aria terziaria (TAD), dove la temperatura varia da 1000 °C nella zona calda a circa 600 °C nella zona fredda, le condizioni operative sono particolarmente difficili. Questo condotto fornisce un flusso d’aria supplementare al processo, non solo migliorando l’efficienza della combustione ma anche permettendo un controllo preciso della temperatura interna del forno. Per garantire prestazioni ottimali, è possibile regolare dinamicamente parametri chiave quali il flusso d’aria, la temperatura e la pressione, grazie a sistemi avanzati di monitoraggio e controllo.
Ambito: Progettazione del rivestimento Fornitura dei materiali refrattari Montaggio del rivestimento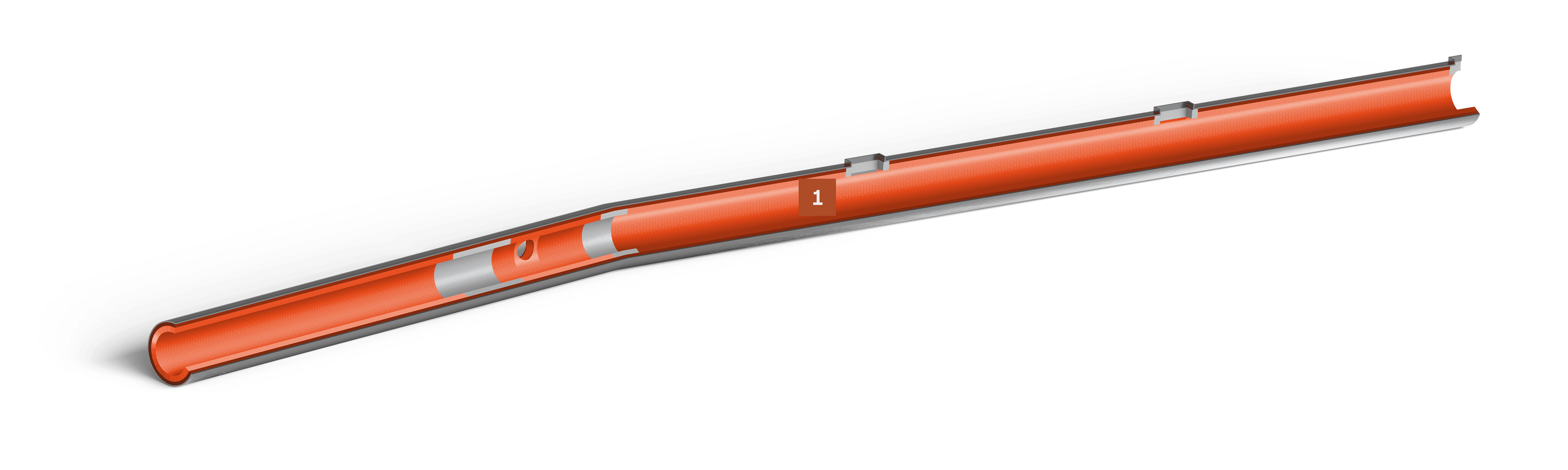
La principale difficoltà legata al rivestimento refrattario del condotto d’aria terziaria è dovuta al suo diametro ridotto, che amplifica l’effetto dell’ambiente abrasivo – le particelle attraversano il condotto ad alta velocità e sotto forte pressione. Per aumentare la durata del rivestimento, PCO consiglia l’uso di mattoni sagomati EXTRATON e calcestruzzi a base di chamotte PCOCAST arricchiti con additivi anti-abrasione come carburo di silicio o zirconio. In condizioni ancora più gravose, quali – pressione o temperatura elevate, – si raccomanda l’impiego di mattoni a base di chamotte con aggiunta di con carburo di silicio della gamma ABRAL.
Come possiamo aiutarti
Se desideri ricevere una consulenza gratuita o porre una domanda sulla scelta del rivestimento refrattario, lasciaci i tuoi dati – ti richiameremo!
ContattaciCome progettare la struttura multistrato del rivestimento per ottenere la temperatura desiderata sul mantello del forno (ad esempio < 200 °C)?
Quale malta refrattaria garantisce la tenuta dei giunti dello strato di lavoro in presenza di alta pressione dell’aria in transito?
Quale materiale è più adatto per il rivestimento delle curve del condotto?
Condotto di risalita e camera d’ingresso al forno
Il condotto di risalita e la camera d’ingresso sono componenti fondamentali del cementificio, responsabili del trasferimento del materiale preriscaldato dai cicloni al forno rotativo, dove la material prima viene ulteriorermente riscaldata. L’intervallo delle temperature di esercizio va da circa 500 °C nella parte superiore del condotto fino a 1100 °C nel punto di ingresso nel forno. Inoltre, la camera d’ingresso (detta anche camera fumi) riceve i gas di scarico caldi in uscita dal forno e li trasferisce nel sistema dei cicloni, consentendo il recupero del calore. I principali fattori di rischio per il corretto funzionamento del rivestimento refrattario in questa zona sono i gas aggressivi (attacchi alcalini), gli urti meccanici e l’abrasione causata dallo scorrimento del materiale, problematiche accentuate negli impianti dotati di calcinatore con elevato uso di combustibili alternativi. Il rivestimento deve quindi essere a bassa porosità e ad alta resistenza all’abrasione. PCO Żarów offre soluzioni complete, dalla progettazione all’installazione, fornendo mattoni e calcestruzzi refrattari con un contenuto di Al₂O₃ compreso tra il 30% e il 60%, arricchiti con additivi che migliorano la resistenza agli agenti chimici e all’abrasione.
Ambito: Progettazione del rivestimento Fornitura dei materiali refrattari Montaggio del rivestimento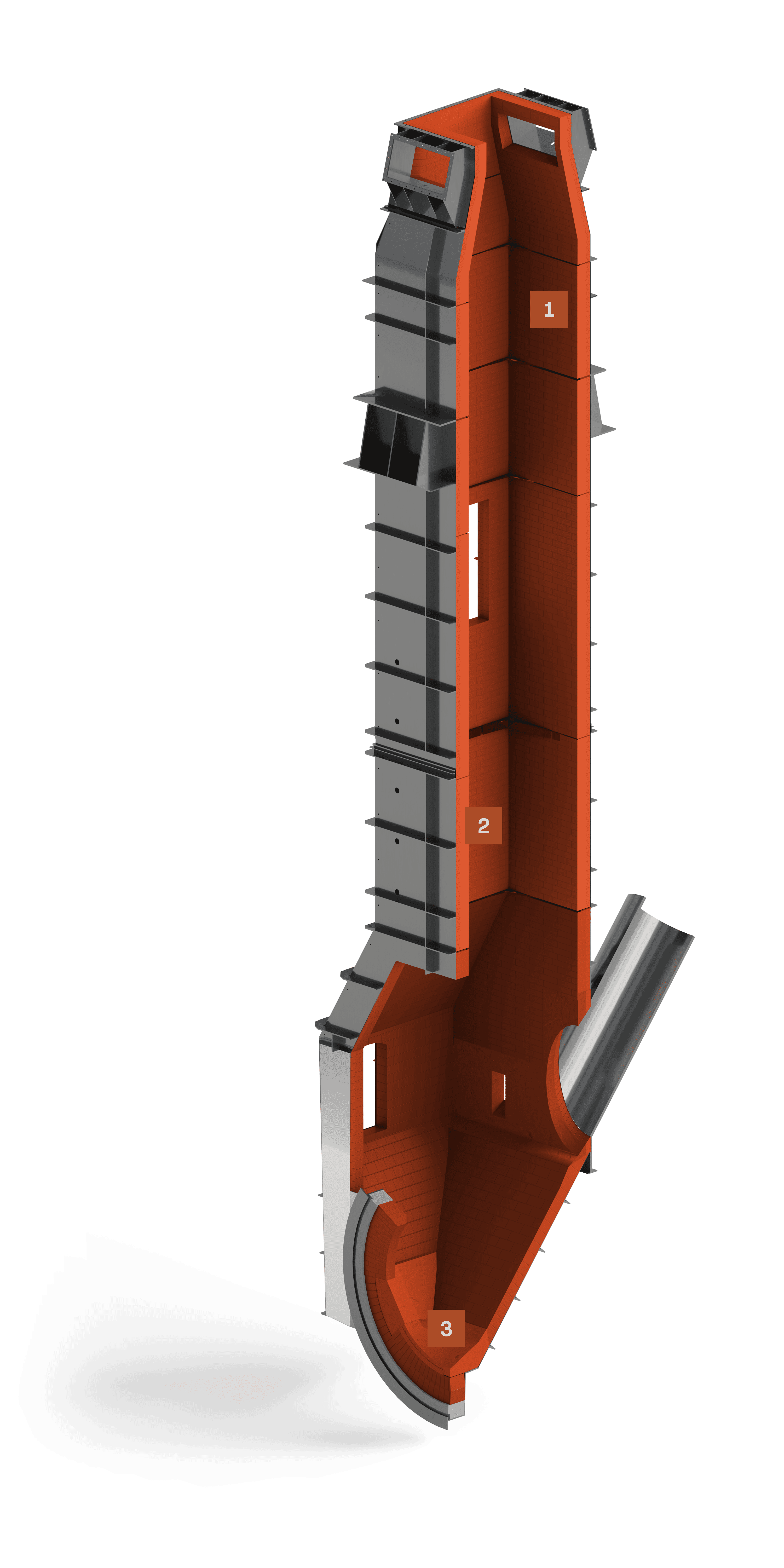
Nella parte superiore del condotto, dove le temperature non superano i 700 °C, si impiegano mattoni a base di chamotte per lo strato di lavoro. PCO Żarów raccomanda i prodotti EXTRATON o ABRAL, che si distinguono per la loro elevata resistenza all’abrasione. In condizioni più impegnative, è possibile utilizzare mattoni ad alto tenore di allumina a base di bauxite – BAUXITEX – che offrono una protezione supplementare.
In questa sezione, caratterizzata da condizioni operative più severe, il rivestimento deve resistere a temperature fino a 1100 °C e ad intensi attacchi chimici. Si utilizzano comunemente materiali ad alto tenore di allumina a base di andalusite o bauxite, integrati con additivi che aumentano la resistenza meccanica e chimica. PCO Żarów raccomanda i prodotti delle gamme ABRAL e, ANDALUX oppure calcestruzzi ultra-basso cemento come NxGel, progettati per precessi di riscaldo rapido e in grado di garantire protezione ottimale in questa zona critica.
La camera d’ingresso (camera fumi) è soggetta principalmente ad attacco chimico da parte dei gas caldi in uscita dal forno. Inoltre, il rivestimento è soggetto a urti meccanici dovuti alla caduta del materiale dal condotto e al suo scorrimento verso il forno rotativo, con conseguente intensa abrasione. Un problema frequente è la formazione di incrostazioni derivanti dalle materie prime, che possono provocare occlusioni el canale. Il rivestimento refrattario deve contenere additivi come carburo di silicio o zirconio per migliorarne la resistenza agli urti e prevenire l’adesione del materiale (grazie a una bassa porosità e bagnabilità), riducendo la formazione di incrostazioni e facilitando il flusso della farina calcarea verso il forno.
Come possiamo aiutarti
Se desideri ricevere una consulenza gratuita o porre una domanda sulla scelta del rivestimento refrattario, lasciaci i tuoi dati – ti richiameremo!
ContattaciQuale materiale migliora la resistenza del rivestimento ai prodotti chimici aggressivi del processo?
Come limitare l’erosione del rivestimento refrattario nella zona di transizione tra il condotto e la camera?
Quale materiale refrattario è più adatto per resistere allo shock termico?
Bruciatore principale
In questa zona, dove la temperatura può superare i 1500 °C, il rivestimento refrattario è sottoposto a rapide variazioni termiche, a radiazione termica e all’azione di ossidanti e composti solforati. Queste condizioni impongono l’impiego di materiali con eccezionale resistenza alla corrosione chimica e allo shock termico. Il rivestimento refrattario del bruciatore non serve solo a proteggere la struttura in acciaio dal deterioramento, ma consente anche una gestione efficace del flusso termico, minimizzando le perdite di calore e aumentando l’efficienza della combustione. In questa zona il rivestimento viene sottoposto a manutenzioni relativamente frequenti – il ciclo di manutenzione varia da pochi mesi fino a un massimo di un anno.
Ambito: Progettazione del rivestimento Fornitura dei materiali refrattari Montaggio del rivestimento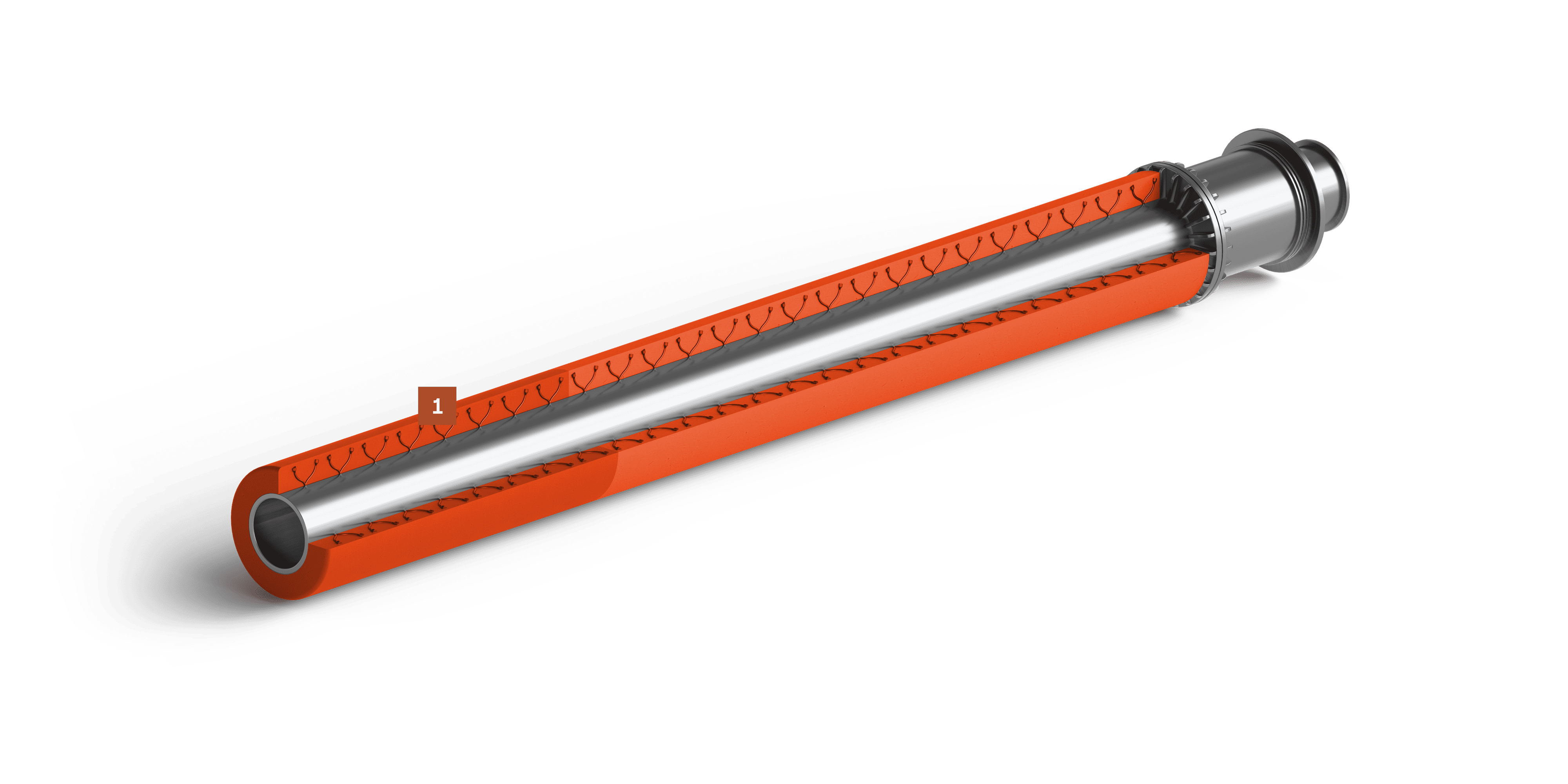
Il rivestimento refrattario in questa zona è esposto a temperature estremamente elevate e all’azione aggressiva dei combustibili alternativi, richiedendo interventi frequenti di riparazione. L’applicazione del rivestimento nella zona di fiamma è particolarmente complessa, soprattutto quandonel processo di applicazione del calcestruzzo direttamente sul bruciatore. Questo richiede non solo tecnologie adeguate, ma anche una notevole esperienza da parte dei muratori. È fondamentale ottenere una consistenza omogenea del calcestruzzo, in modo da garantire una distribuzione uniforme del materiale e un riscaldamento rapido, indispensabile per mantenere la continuità operativa del forno. A causa delle condizioni di lavoro estreme presenti nella zona della fiamma, il materiale refrattario deve possedere una resistenza molto elevata sia agli shock termici sia all’azione aggressiva dei combustibili alternativi.
Come possiamo aiutarti
Se desideri ricevere una consulenza gratuita o porre una domanda sulla scelta del rivestimento refrattario, lasciaci i tuoi dati – ti richiameremo!
ContattaciCome progettare gli elementi prefabbricati del bruciatore per evitarne il surriscaldamento?
Quale materiale refrattario è più indicato per resistere alle sollecitazioni termiche della zona di fiamma?
Come pianificare il ciclo di ispezioni del rivestimento del bruciatore per individuare tempestivamente un’usura eccessiva?
Forno rotante
Il ruolo principale del forno rotativo nel processo di produzione del clinker è quello di riscaldare le materie prime a temperature molto elevate (1350–1450 °C), provocandone la calcinazione e le reazioni chimiche necessarie alla formazione dei minerali del clinker. Le cause pricipali di usura del rivestimento refrattario del forno comprendono: abrasione, sollecitazioni termiche derivanti sia dal materiale in carica sia dal bruciatore, carichi meccanici causati dalla rotazione della struttura in acciaio del forno, corrosione chimica dovuta al contatto con la carica, con i gas di combustione e con le scorie derivanti dall’uso di combustibili alternativi, la presenza l’attacco di composti chimici aggressivi. Per i forni rotanti, PCO offre una gamma completa di materiali e servizi. La nostra offerta comprende refrattari ad alto tenore di allumina con aggiunta di carburo di silicio – caratterizzati da una maggiore resistenza alla corrosione chimica, all’abrasione e agli shock termici – prodotti a base di andalusite con legante chimico di lunga durata, mattoni in chamotte e ad alto tenore di allumina progettati per condizioni di forte usura e ambienti chimicamente aggressivi.
Ambito: Progettazione del rivestimento Fornitura dei materiali refrattari Montaggio del rivestimento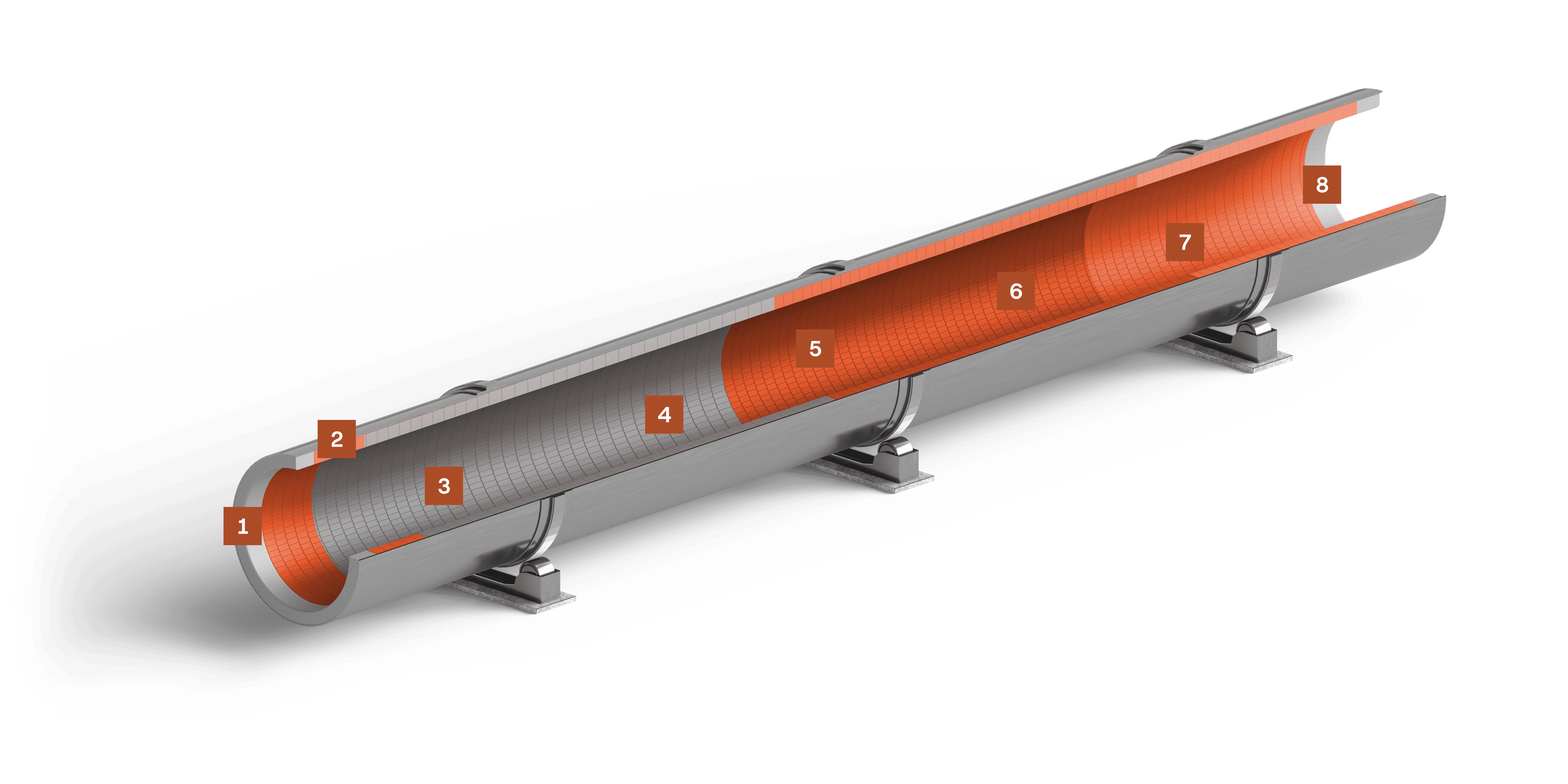
La zona terminale del forno – detta "Nose Ring" – presenta condizioni simili a quelle della zona di uscita. Le temperature sono variabili e la carica esercita pressioni meccaniche elevate, il che richiede l’utilizzo di materiali con ottima resistenza meccanica. La struttura del forno rotativo prevede l’impiego di prodotti monolitici, colati in opera durante la manutenzione. Le proprietà fondamentali di questi materiali sono la resistenza alla compressione e all’abrasione, garantendo l’integrità strutturale in condizioni di carico intenso. Sono raccomandati calcestruzzi ad alto tenore di allumina della linea MULCAST e calcestruzzi a basso contenuto di cemento della linea PCOCAST.
Nella zona di raffreddamento, , la sfida principare per i materiali refrattari è l’urto meccanico, causato dalla frammentazione del clinker che, cambia il proprio volume a casua dei rapidi sbalzi di temperatura. Le temperature variano tra 900 °C e 1100 °C. Il rivestimento è composto da uno strato unico di mattoni a cuneo, e le caratteristiche fondamentali richieste ai materiali refrattari sono un’elevata resistenza allo shock termico e un’ottima resistenza meccanica agli urti e all’abrasione.
In questa zona il clinker sinterizzato si raffredda gradualmente, con temperature che scendono fino a circa 1200 °C. Nonostante la ridotta temperatura, si continuano ad utilizzare materiali refrattari resistenti a variazioni termiche dinamiche. In questa zona prevalgono i prodotti a base di magnesite e spinello, che garantiscono protezione continua del rivestimento e limitano le sollecitazioni termiche.
La zona di cottura è l’area in cui si raggiungono le temperature più elevate – fino a 1500 °C – e dove avvengono le trasformazioni chimiche complete. La carica calcarea è sottoposta a intense reazioni che portano alla formazione dei minerali del clinker. In questa zona si consigliano materiali a base di magnesite, che offrono un’eccellente resistenza alle condizioni termiche e chimiche estreme del processo di combustione.
Qui si registrano sollecitazioni termiche molto intense, con temperature che superano i 1200 °C. Le condizioni sono instabili e variabili, e il rivestimento – composto da uno strato unico di mattoni a cuneo – deve resistere a rapide variazioni di temperatura. In questa zona si usano prevalentemente prodotti in magnesite-spinello, mentre al confine con la zona di sicurezza si installano materiali silico-alluminosi di altissima qualità, per una protezione ottimale contro gli shock termici.
In questa zona le temperature superano i 1000 °C e favoriscono la decomposizione del calcare. Le condizioni operative sono variabili e fortemente influenzate dal processo, soprattutto quando aumenta la quota di CSS nel combustibile. Il rivestimento – composto da uno strato unico di mattoni a cuneo – è esposto ad attacchi alcalini, liquidi eutettici, sollecitazioni instabili e a un’aggressione chimica e termica continua. La scelta del materiale refrattario deve essere flessibile per adattarsi alle condizioni specifiche. Si utilizzano prodotti ad alto tenore di allumina con additivi in carburo di silicio – come ABRAL o ANDALUX – oppure BAUXITEX con a legame chimico
In questa zona, oltre all’intensa abrasione meccanica causata dal movimento della carica, si verifica un'ulteriore azione di composti alcalini derivanti dalle materie prime e dai combustibili. Le temperature si mantengono tra 1000 e 1100 °C. Il rivestimento è costituito da uno strato unico di mattoni a cuneo. Le caratteristiche richieste sono alta resistenza meccanica e alla corrosione, per garantire il funzionamento continuo anche in presenza di condizioni di processo variabili. In questa applicazione si utilizzano con successo i prodotti della linea ABRAL, noti per l’elevata resistenza all’usura chimica e meccanica.
Questa zona rappresenta l’inizio del rivestimento del forno ed è soggetta ad abrasione meccanica intensa causata dallo scorrimento della carica. Per affrontare questa sfida, si utilizzano calcestruzzi refrattari resistenti all’usura. È essenziale impiegare calcestruzzi ad alto tenore di allumina; i prodotti consigliati sono i calcestruzzi a medio contenuto di cemento della linea MULCAST oppure i calcestruzzi privi di cemento GELCAST, entrambi in grado di offrire sufficiente resistenza e durata contro l’usura meccanica.
Come possiamo aiutarti
Se desideri ricevere una consulenza gratuita o porre una domanda sulla scelta del rivestimento refrattario, lasciaci i tuoi dati – ti richiameremo!
ContattaciCome ottimizzare la scelta dei formati e la disposizione dei mattoni per ridurre la formazione di anelli e incrostazioni di clinker?
Quale materiale refrattario è più adatto in un forno alimentato con un’elevata percentuale di CSS?
Come progettare il rivestimento tenendo conto della geometria irregolare dello scheletro?
Raffreddatore e cappa del forno
Il raffreddatore e la cappa del forno (Kiln hood) hanno la funzione di raffreddare il clinker all’uscita del forno rotante. Nella kiln hood le temperature possono raggiungere i 1100 °C, mentre nel raffreddatore scendono gradualmente – da circa 800 °C nella zona calda fino a circa 100 °C nella zona fredda. La struttura del raffreddatore è suddivisa in: zona calda, zona fredda, volta e bullnose ring. In tutte le aree del raffreddatore si impiegano materiali refrattari silico-alluminosi. L’usura del rivestimento della cappa del raffreddatore è causata principalmente da shock termici dovuti alla frantumazione del clinker e dall’abrasione derivante dal suo movimento. Ulteriori rischi sono rappresentati dagli shock termici e dall’azione chimica e abrasiva dei gas di processo. La zona più esposta all’usura è il bullnose, collocato a diretto contatto sia con i gas ad alta temperatura sia con il clinker. PCO propone una vasta gamma di materiali refrattari per il rivestimento dei raffreddatori, tra cui calcestruzzi refrattari, elementi prefabbricati in calcestruzzo e mattoni in bauxite.
Ambito: Progettazione del rivestimento Fornitura dei materiali refrattari Montaggio del rivestimento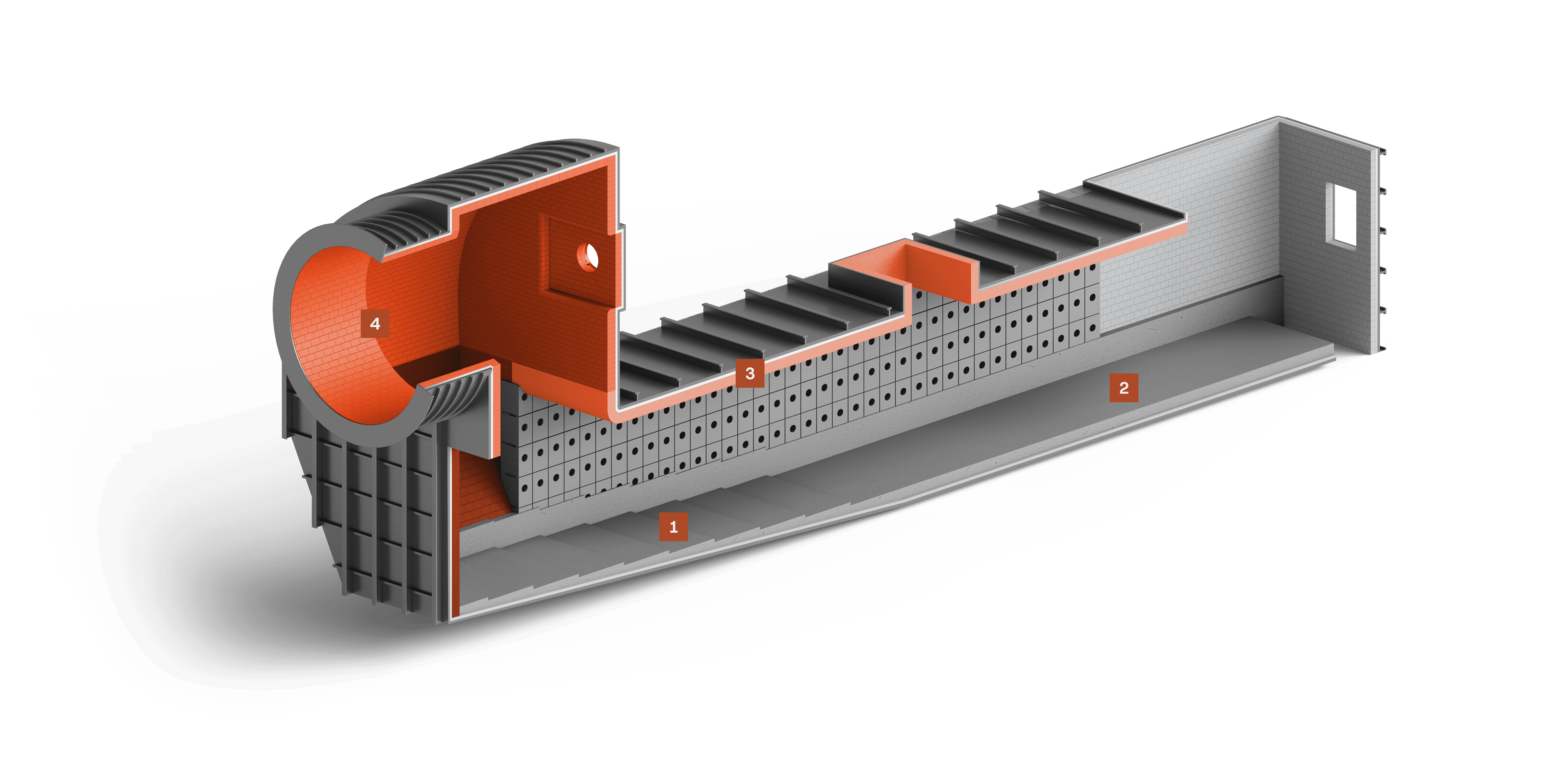
Nella zona calda del raffreddatore le temperature possono raggiungere i 1000 °C, ma calano bruscamente in prossimità della griglia mobile. Queste condizioni generano forti shock termici. Sul letto di clinker, la principale minaccia per il rivestimento refrattario è l’abrasione meccanica intensa, causata sia dallo spostamento del materiale sia dai flussi dinamici di aria e polveri. Il rivestimento viene realizzato con elementi prefabbricati in calcestruzzo, chiamati muretti di contenimento, che offrono sia isolamento termico efficace sia stabilità meccanica in condizioni termiche variabili. Un aspetto fondamentale per la durata del rivestimento è l’impiego di calcestruzzo ad alto tenore di allumina, caratterizzato da ottima resistenza agli shock termici e all’abrasione. Questo materiale mantiene le sue proprietà operative anche in presenza di rapidi cali di temperatura e sollecitazioni meccaniche elevate.
La zona fredda del raffreddatore è caratterizzata da condizioni termiche molto stabili, con temperature che non superano i 500 °C. Grazie all’azione più mite delle temperature e alle minori variazioni dinamiche, questa parte del raffreddatore presenta un basso stress termico meccanico he si traduce in una minore frequenza degli interventi di manutenzione. Il rivestimento viene realizzato con calcestruzzo a spruzzo, che garantisce una superficie uniforme e continua. Inoltre, lungo la griglia vengono si installano muretti di contenimento prefabbricati, realizzati con refrattari di qualità specifica, come MULCAST BN45M S5.
La volta, presente sia nella zona calda che in quella fredda, è soggetta ad abrasione provocata da polveri volatili e a rapide variazioni termiche lungo tutta la lunghezza del raffreddatore. I materiali refrattari devono resistere sia all’usura meccanica sia agli sbalzi termici. Nella zona calda è fondamentale utilizzare materiali con ottime proprietà meccaniche e termiche, in particolare con aggiunta di SiC per rafforzare la resistenza del rivestimento. Nelle zone fredde, la priorità è mantenere coesione e durabilità del rivestimento anche a temperature inferiori, permettendo un esercizio prolungato senza necessità di manutenzione frequente.
La funzione principale della cappa del forno (kiln hood) è raccogliere il clinker e trasferirlo al raffreddatore, in condizioni di forte sollecitazione meccanica e termica. Particolare attenzione va prestata alla zona denominata "bullnose" – una parete verticale tra le più vulnerabili. Il rivestimento refrattario in questa zona è sottoposto a sollecitazioni meccaniche causate dagli impatti del clinker in caduta e a improvvisie variazioni di temperatura, che richiedono materiali altamente performanti. Il rivestimento del kiln hood è forno viene realizzato solitamente con mattoni sagomati, che garantiscono stabilità termica e isolamento adeguato, riducendo le perdite di calore e l’influenza dei fattori esterni. Per il bullnose ring, invece, data l’intensità delle sollecitazioni meccaniche, si impiegano calcestruzzi refrattari di alta qualità o prefabbricati in calcestruzzo.
Come possiamo aiutarti
Se desideri ricevere una consulenza gratuita o porre una domanda sulla scelta del rivestimento refrattario, lasciaci i tuoi dati – ti richiameremo!
ContattaciQuale calcestruzzo refrattario garantisce la massima resistenza all’abrasione nella zona del bullnose ring?
Come prevenire danni al rivestimento causati da shock termici durante le fluttuazioni del flusso dei gas più freddi?
Come progettare muretti di contenimento prefabbricati per proteggere il rivestimento dalle vibrazioni della griglia?
Forno verticale per calce
Il forno verticale, impiegato nella produzione della calce, funziona a temperature che spesso superano i 1100 °C. Il processo di calcinazione richiede una distribuzione del calore omogenea e controllata lungo tutta l’altezza del forno. La pietra calcarea, introdotta nel forno insieme a coke o antracite, viene sottoposta a combustione, generando calore sufficiente per trasformarla in calce viva (ossido di calcio, CaO). Nel settore della soda, i forni operano a temperature leggermente inferiori rispetto alla produzione classica di calce, comportando requisiti meno severi per i materiali refrattari e i sistemi di riscaldamento. Nelle zuccherifici, invece, i forni devono affrontare condizioni specifiche, con frequenti variazioni di temperatura e arresti. Ciò richiede materiali refrattari resistenti ai cicli termici, in grado di sopportare ripetute dilatazioni senza usura eccessiva. Nei forni di questo tipo, la calcinazione non avviene in modo continuo, a differenza di quanto accade nei settori industriali della calce e della soda.
Ambito: Progettazione del rivestimento Fornitura dei materiali refrattari Montaggio del rivestimento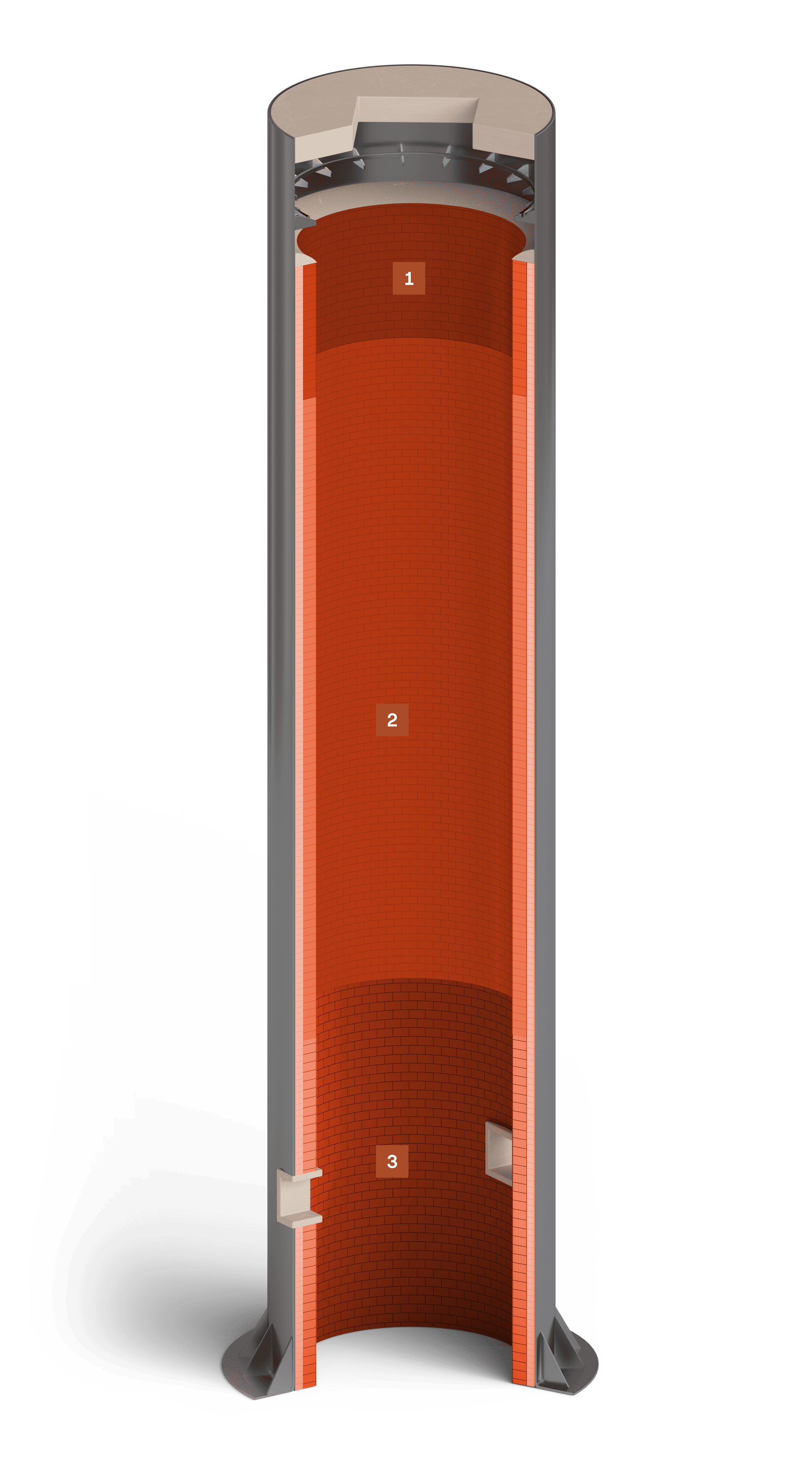
Questa è l’area in cui la pietra calcarea mescolata al combustibile viene caricata ciclicamente. Il processo genera un’usura abrasiva intensa dovuta al movimento meccanico della carica, unita a temperature elevate. I materiali impiegati devono offrire un’elevata resistenza all’abrasione – per questo si utilizzano prodotti allumino-silicatici EXTRATON. Inoltre, per ridurre le perdite termiche, si applica uno strato isolante composto da prodotti ISOLUX abbinati a lana minerale, ottenendo ottime prestazioni di isolamento termico. È fondamentale combinare proprietà meccaniche e isolanti per garantire la durabilità del rivestimento e il corretto bilancio termico del forno.
Questa zona, spesso identificata con quella di calcinazione, è dove si svolge l’intensa reazione di cottura della carica, ad esempio della pietra calcarea o dolomitica. La temperatura e la composizione della carica determinano le specifiche interazioni chimiche e termiche, compreso il rischio di idratazione. In condizioni normali, Al₂O₃ e SiO₂ sono stabili chimicamente, ma è essenziale scegliere materiali che mantengano stabilità anche in presenza di umidità. I prodotti MULITEX, ANDALUX o BAUXITEX sono ideali per questa zona, poiché garantiscono elevata resistenza all’idratazione e stabilità chimica a temperature elevate.
In questa zona, il rivestimento è soggetto a un abbassamento progressivo della temperatura, comportando sollecitazioni termiche meno intense, ma richiedendo comunque resistenza all’abrasione. Nei forni a colonna singola, il raffreddamento avviene in modo uniforme lungo tutta l’altezza, consentendo l’uso di soluzioni isolanti omogenee. I materiali chamottati, in particolare i prodotti SUPERTON, sono ideali grazie alla loro buona resistenza alla compressione e all’abrasione. Lo strato isolante, lungo tutta l’altezza del forno, è composto da moduli ISOLUX integrati con lana minerale, formando una barriera termica continua e affidabile.
Come possiamo aiutarti
Se desideri ricevere una consulenza gratuita o porre una domanda sulla scelta del rivestimento refrattario, lasciaci i tuoi dati – ti richiameremo!
ContattaciQuali mattoni ad alto tenore di allumina resistono meglio alla degradazione chimica causata da esposizione prolungata al CO₂ nell’atmosfera del forno?
Quali miscele da spruzzo o da ramming offrono la migliore resistenza alla disgregazione e all’attacco di vapore derivante da carica umida?
Come ottimizzare la forma dei mattoni, la progettazione delle ancore metalliche e la configurazione dei giunti in forni ad alta colonna per gestire la dilatazione termica assiale ed evitare cedimenti del rivestimento?
Forno Maerz – panoramica delle soluzioni
Il forno Maerz, utilizzato in processi che richiedono un controllo preciso della temperatura e una distribuzione uniforme del calore, funziona in condizioni in cui i rivestimenti refrattari ceramici sono esposti a temperature molto elevate, spesso superiori ai 1200 °C. Una caratteristica distintiva dei forni Maerz rispetto agli altri forni verticali è il principio della reversione, fondamentale per il loro funzionamento. Il forno è composto da due colonne: una destinata alla calcinazione della pietra calcarea e l’altra all’alimentazione dell’aria comburente. Il principio di reversione consiste nell’invertire ciclicamente le fasi di combustione e calcinazione, permettendo un controllo termico più efficiente e un migliore utilizzo dell’energia, grazie a una gestione alternata dei flussi gassosi. Poiché i forni Maerz offrono maggiore produttività e sono sottoposti a condizioni operative più complesse rispetto ai forni verticali convenzionali, è necessario impiegare materiali refrattari di qualità superiore. Questi devono garantire eccellente resistenza agli shock termici e all’erosione chimica, per mantenere l’integrità del rivestimento anche in presenza di forti variazioni operative. L’ottimizzazione della distribuzione del calore e la riduzione delle perdite termiche sono essenziali per assicurare l’efficienza del processo e la durabilità dell’impianto.
Ambito: Progettazione del rivestimento Fornitura dei materiali refrattari Montaggio del rivestimento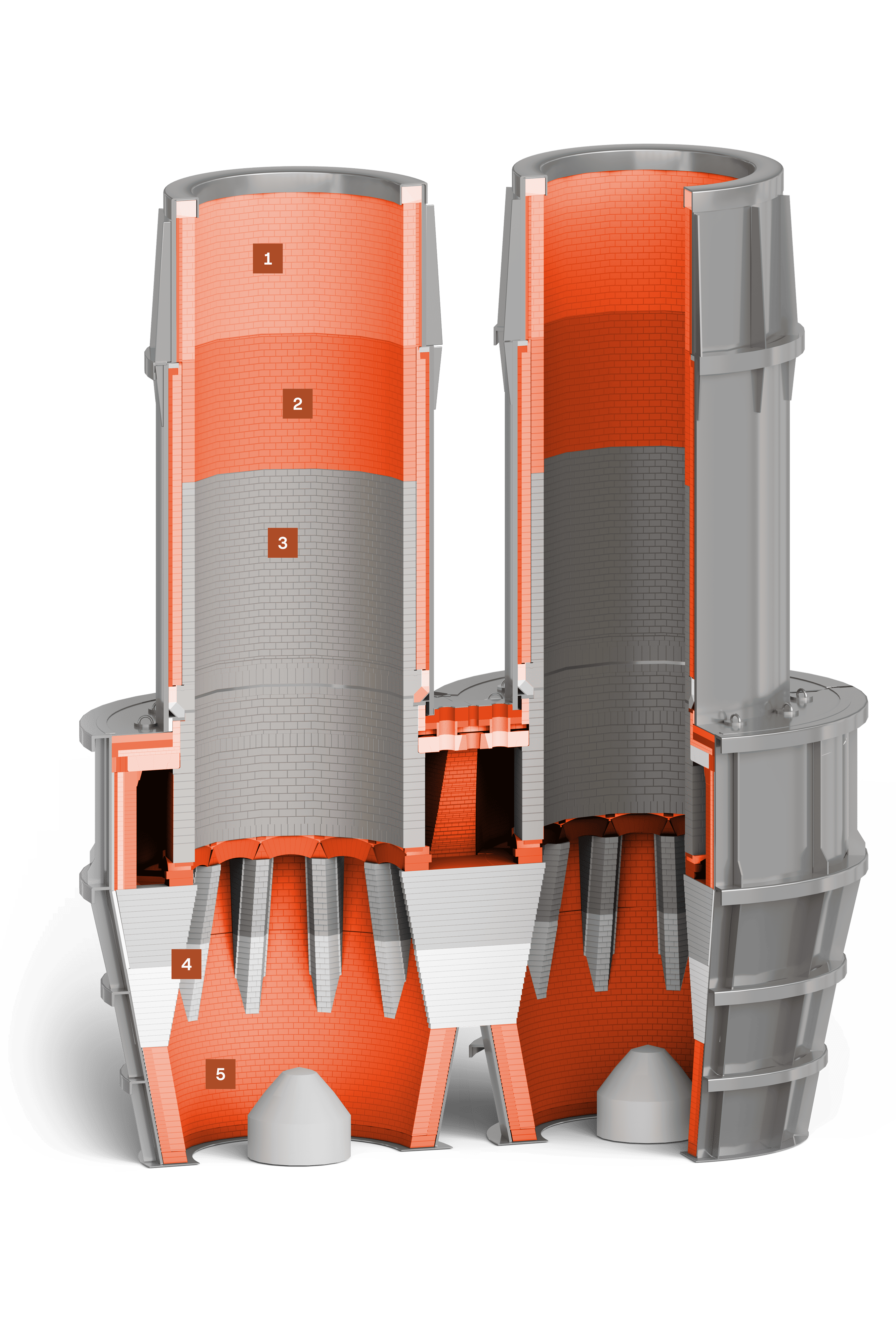
Questa zona si estende dal livello inferiore dei bruciatori alla parte alta del forno, dove la pietra calcarea miscelata al combustibile viene caricata ciclicamente. Qui si verifica una forte abrasione meccanica e un’intensa sollecitazione termica, dovute al contatto diretto tra la carica e il rivestimento e alle fluttuazioni di temperatura. Per garantire la durata e l’efficienza del forno, è essenziale impiegare materiali resistenti all’usura e con buone capacità isolanti. Nella parte inferiore, in prossimità dei bruciatori, si utilizzano prodotti magnesia-spinello, resistenti all’abrasione e agli agenti aggressivi generati dalla combustione. Nella parte superiore della colonna si impiegano invece materiali allumino-silicatici ad alta resistenza all’usura, come quelli della linea EXTRATON.
Per consentire un passaggio graduale tra lo strato magnesia-spinello e quello allumino-silicatico, si inserisce una zona di transizione realizzata con materiali ad alto tenore di allumina (andalusitici). Lo spazio tra l’involucro in acciaio e lo strato di lavoro viene riempito con un sistema isolante, composto da pannelli ISOLUX e materassini in lana minerale. In alcuni casi si prevede un ulteriore strato isolante in prodotti SUPERTON o EXTRATON, posto tra lo strato di lavoro e l’isolamento principale. L’intero rivestimento della colonna termina con uno strato in calcestruzzo convenzionale, che funge da finitura e protezione strutturale.
La zona di cottura si estende dal livello inferiore delle volte portanti fino al livello inferiore dei bruciatori (lance a gas). In questa parte del forno la carica subisce una calcinazione intensiva, generando temperature molto elevate e condizioni chimicamente aggressive, variabili in funzione del tipo di pietra trattata (calcarea o dolomitica). PCO Żarów fornisce i materiali per lo strato protettivo e isolante di questa zona. L’intero rivestimento della colonna, a partire dalla zona di dilatazione, è realizzato con pezzi sagomati speciali (tipi AS1, AS2 e simili), prodotti con materiali delle gamme MULITEX o ANDALUX, garantendo stabilità strutturale e resistenza a condizioni di esercizio variabili.
La struttura del forno Maerz comprende pilastri, volte tra i pilastri, volte piane e un canale di collegamento, tutti realizzati in calcestruzzi a basso contenuto o privi di cemento. La costruzione dei pilastri richiede l’utilizzo combinato di pezzi sagomati tipo VK-76x e WL-76, che assicurano un’elevata stabilità meccanica. Nei forni Maerz senza pilastri, anche la base del cilindro sospeso è costruita con calcestruzzi resistenti. Sulle volte piane viene applicato uno strato isolante in calcestruzzo leggero tipo ISOCAST o ISOGUN, completato da lana minerale.
Questa zona si estende dal primo livello del rivestimento fino al livello inferiore delle volte tra i pilastri. In questa sezione la temperatura si riduce progressivamente, stabilizzando il processo di raffreddamento. Nonostante il calo termico, il rivestimento è comunque soggetto ad abrasione e sollecitazioni meccaniche, dovute sia al movimento del materiale che agli sforzi termici. Lo strato di lavoro è realizzato con prodotti chamottati – SUPERTON o EXTRATON – ideali per queste condizioni. Le zone tra i pilastri vengono generalmente rivestite con mattoni EXTRATON. Lo strato isolante è composto da moduli ISOLUX, pannelli in silicato di calcio e materassini in lana minerale, creando una barriera termica continua.
Come possiamo aiutarti
Se desideri ricevere una consulenza gratuita o porre una domanda sulla scelta del rivestimento refrattario, lasciaci i tuoi dati – ti richiameremo!
ContattaciQuale geometria dei blocchi dei pilastri può migliorare la resistenza meccanica del rivestimento?
Quali materiali refrattari resistono meglio alla combinazione di abrasione e aggressione chimica durante la calcinazione della pietra calcarea?
Come progettare gli strati di transizione e protezione tra materiali basici e allumino-silicatici per gestire le dilatazioni termiche cicliche senza danneggiare il rivestimento?
Forno rotativo per la produzione di calce e pasta di cellulosa
Il forno rotativo per calce, utilizzato nel processo Kraft, consente il recupero della calce dalla sospensione calcarea per il successivo utilizzo nella produzione di cellulosa. Il rivestimento refrattario di questi forni è generalmente composto da due strati, garantendo sia durabilità che resistenza alle condizioni operative estreme. I principali fattori di rischio per il rivestimento sono le rapide variazioni di temperatura, l’interazione chimica con la sospensione calcarea, e le sollecitazioni di pressione e stress causate dalla rotazione del forno. A seconda delle zone, vengono utilizzati diversi tipi di materiali refrattari. Nella zona d’ingresso e di uscita del forno si impiegano calcestruzzi refrattari altamente resistenti agli shock termici e alla corrosione chimica, oltre a mattoni chamottati e andalusitici. Nella zona di cottura si preferiscono mattoni andalusitici arricchiti con P₂O₅, in grado di resistere a temperature estreme, ad agenti chimici aggressivi e a elevate sollecitazioni meccaniche.
Ambito: Progettazione del rivestimento Fornitura dei materiali refrattari Montaggio del rivestimento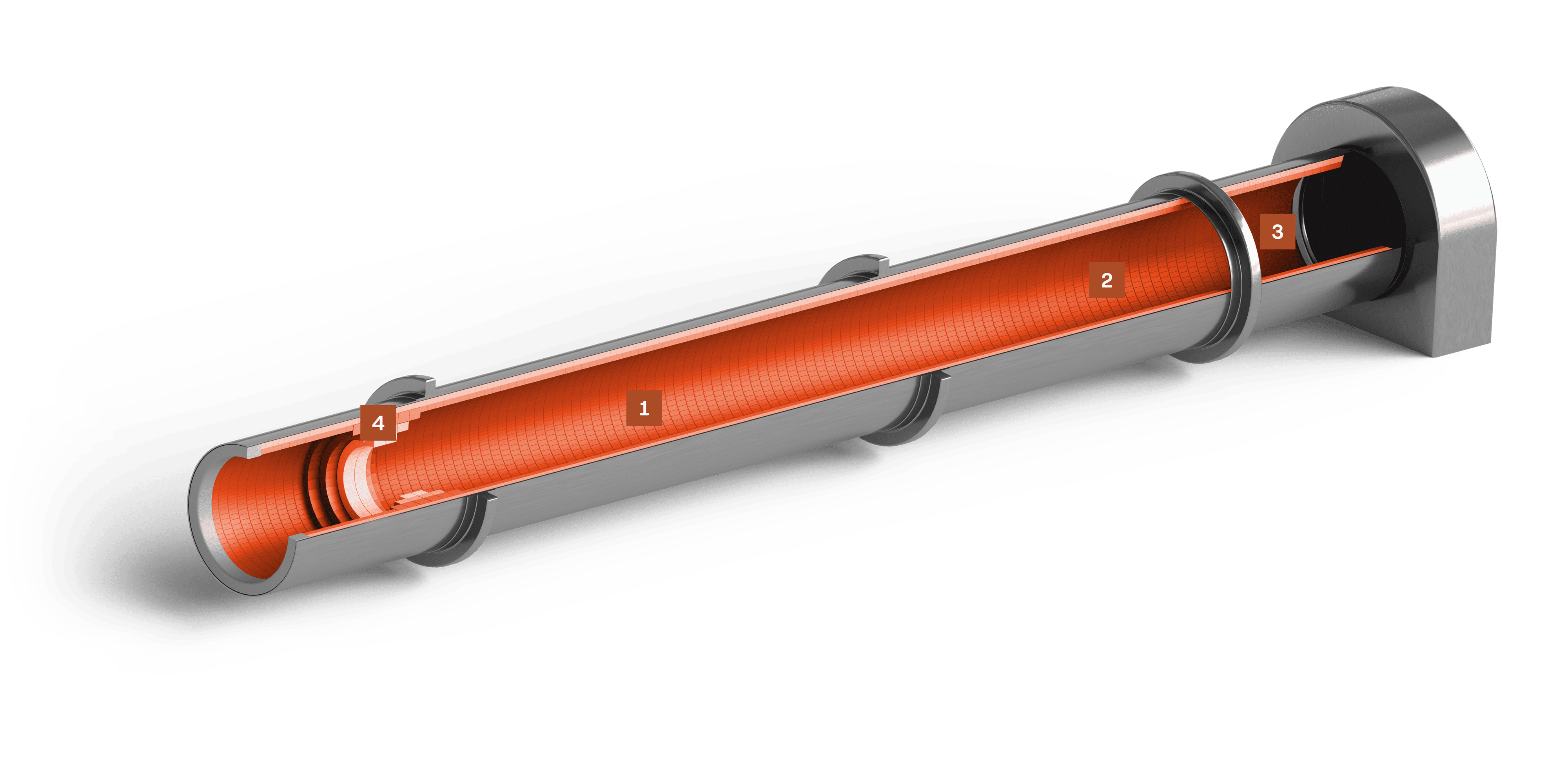
Questa zona copre l’aumento della temperatura da circa 200 °C a 1100 °C. Qui la sospensione viene essiccata e parzialmente calcinata. Il rivestimento è soggetto ad abrasione e a erosione chimica. La sospensione contiene sali alcalini, composti solforati e cloruri, che rappresentano un rischio di infiltrazione chimica. Inoltre, la carica è umida (fino al 20 %), quindi il rivestimento deve resistere alla penetrazione dell’acqua nei pori. Per lo strato di lavoro si consigliano mattoni chamottati di alta qualità, a bassa porosità e resistenti agli alcali – come quelli della linea EXTRATON. Nelle aree più vicine alla zona di cottura, dove le temperature sono più elevate, si possono impiegare mattoni ad alto tenore di allumina o con legante chimico – come quelli della gamma ANDALUX.
In questa zona le temperature variano tra 1100 °C e 1300 °C lungo tutta la sua estensione. Le condizioni operative sono variabili, con sollecitazioni termiche provenienti dalla fiamma del bruciatore e stress chimico da parte dei gas di processo. La sospensione calcarea subisce sinterizzazione e trasformazione da fanghiglia contenente carbonati a CaO puro (calce viva). Il rivestimento refrattario deve resistere allo shock termico, all’alta temperatura, e alla corrosione chimica e meccanica. Lo strato è a doppia struttura; per lo strato di lavoro si raccomandano mattoni andalusitici con legante chimico della linea ANDALUX.
È la sezione più corta del forno, che si estende per alcuni metri prima dell’ingresso nel raffreddatore. Qui la temperatura cala bruscamente da 1000 °C a circa 200 °C, generando forti shock termici. In questa fase la calce è già formata e agisce abrasivamente sul rivestimento durante lo spostamento. La rotazione del forno e la geometria a restringimento (riduzione del diametro) causano sollecitazioni meccaniche critiche. Il rivestimento è a doppio strato: nei restringimenti si utilizza calcestruzzo refrattario ad alto tenore di allumina per lo strato di lavoro, mentre per l’isolamento si impiegano pannelli sagomati ISOLUX con alta resistenza alla compressione.
La soglia di carico è realizzata in ceramica refrattaria e serve a uniformare la distribuzione della carica all’uscita del forno. Il rivestimento in questa zona è soggetto a forte abrasione e stress meccanico. Si consigliano mattoni andalusitici di altissima qualità, capaci di regolare il flusso della carica in modo efficiente.
Come possiamo aiutarti
Se desideri ricevere una consulenza gratuita o porre una domanda sulla scelta del rivestimento refrattario, lasciaci i tuoi dati – ti richiameremo!
ContattaciQuale materiale è adatto come rivestimento di lavoro a contatto con catrame e acidi organici?
Come proteggere il rivestimento da fessurazioni causate dalla diversa dilatazione tra la corazza metallica, lo strato isolante e quello di lavoro?
Come rilevare l’usura eccessiva del rivestimento nelle aree soggette ad accumulo di depositi o vicino al bruciatore?
Perché PCO?
Installazione inclusa con la fornitura dei refrattari – gestione del progetto più semplice e un unico garante della qualità.
Gamma completa di prodotti refrattari allumino-silicatici per i settori del cemento, della calce e della carta.
Un team interno di progettisti e ingegneri pronto ad affrontare ogni sfida.
Prodotti e servizi selezionati
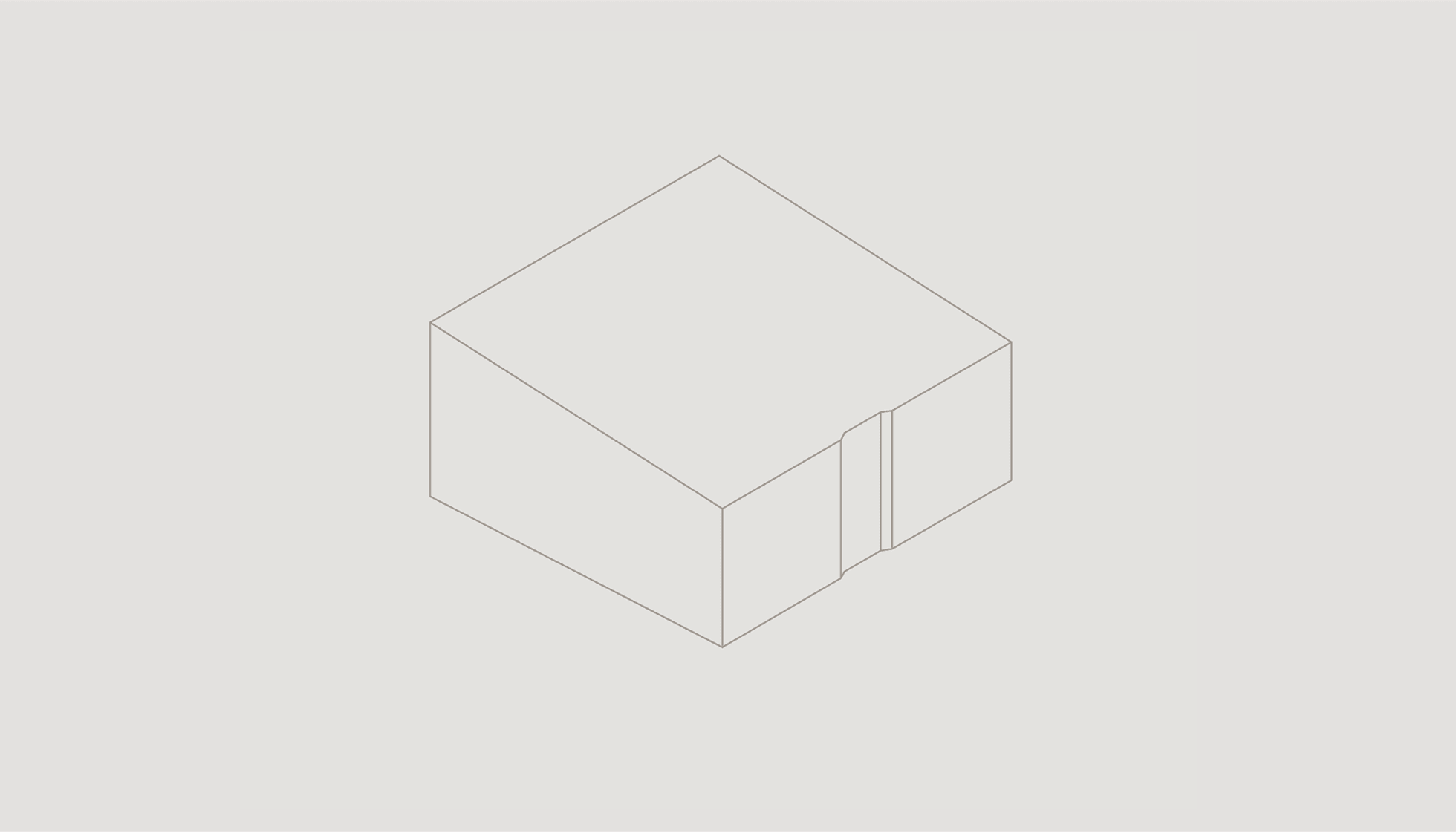
Linea di prodotti ABRAL
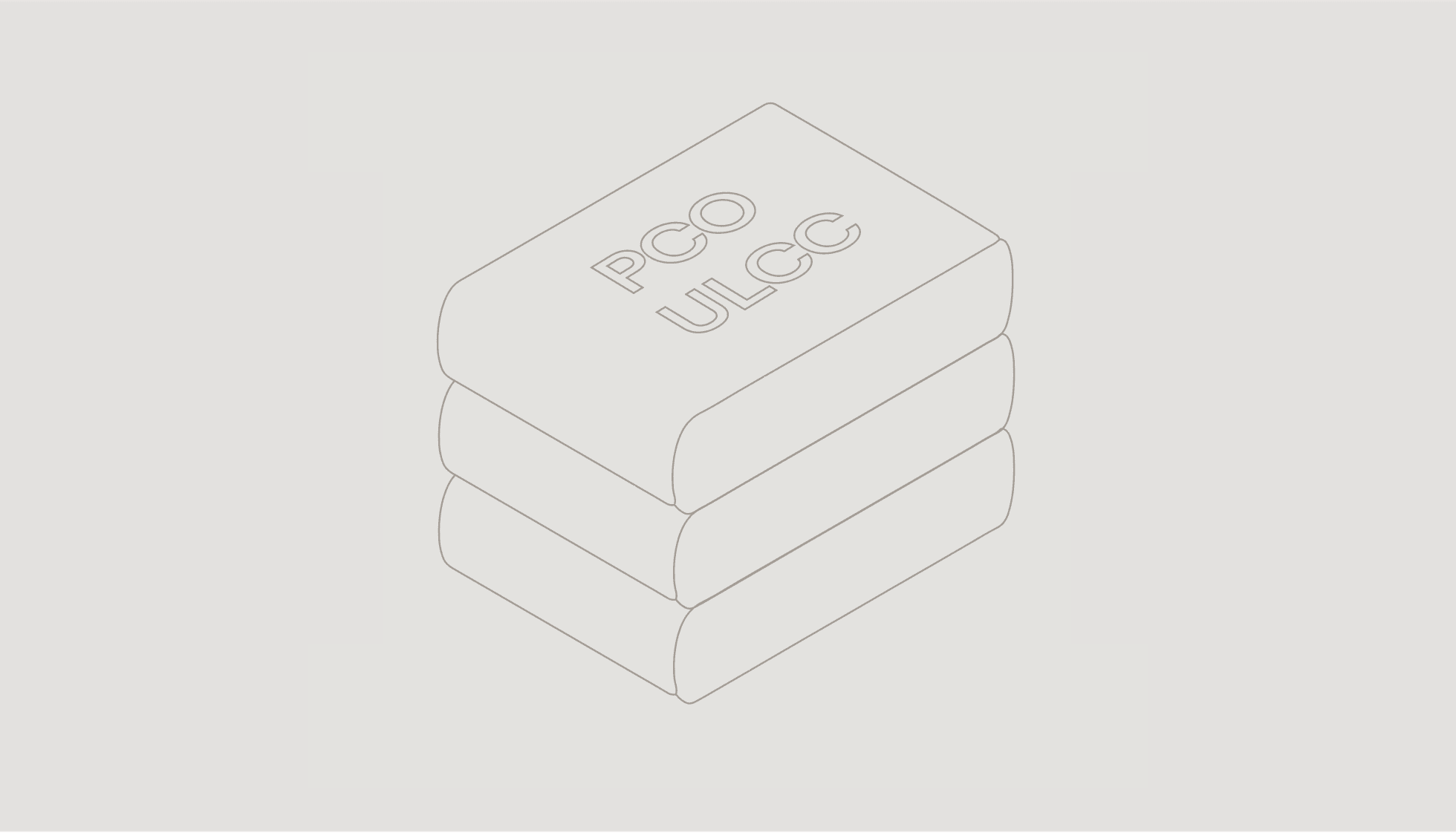
Calcestruzzi refrattari ULCC (Ultra Low Cement Castables)
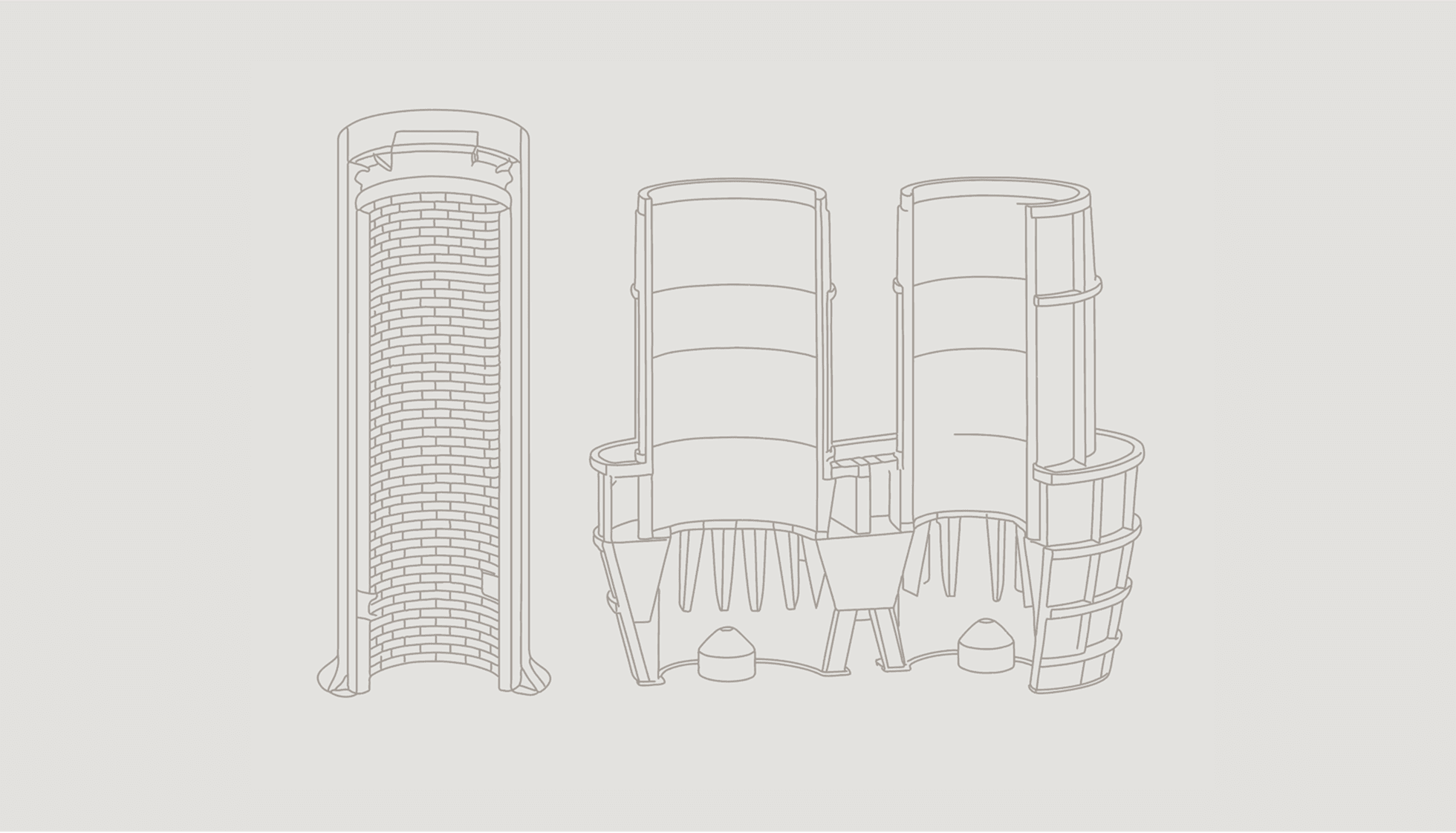
Supervisione per il rivestimento di forni verticali e forni Maerz
Contattaci
Si prega di selezionare l'opzione che descrive meglio l'argomento che si desidera discutere con noi. Questo ci aiuterà ad indirizzare la tua richiesta alla persona giusta presso PCO.