Acciaieria
La nostra offerta per l’industria siderurgica
Sebbene i materiali refrattari rappresentino una piccola parte dei costi complessivi di produzione del ferro e dell’acciaio, la loro affidabilità è fondamentale per l’efficienza dei processi produttivi.
Un supporto adeguato nella tecnologia refrattaria può prolungare gli intervalli tra le manutenzioni, ridurre i costi di riparazione e migliorare l’efficienza energetica del processo, contribuendo al raggiungimento degli obiettivi di sostenibilità. La nostra missione è affiancare i nostri partner nella tecnologia refrattaria esattamente dove le loro organizzazioni ne hanno bisogno: dagli studi di ingegneria alla selezione congiunta delle soluzioni materiali e delle tecnologie di installazione più efficaci, fino alla logistica in qualsiasi parte del mondo, all'installazione o alla sua supervisione e al supporto post-installazione. Crediamo che la qualità e l'affidabilità dei nostri prodotti e servizi, unite a un supporto completo, contribuiranno a minimizzare i tempi di fermo produzione e a rendere i nostri partner più competitivi e sostenibili grazie alla nostra tecnologia refrattaria! Scopri la nostra offerta completa per il settore siderurgico, che comprende un’ampia gamma di servizi e prodotti: mattoni e calcestruzzi in chamotte, andalusite, mullite e alto allumina, nonché materiali isolanti.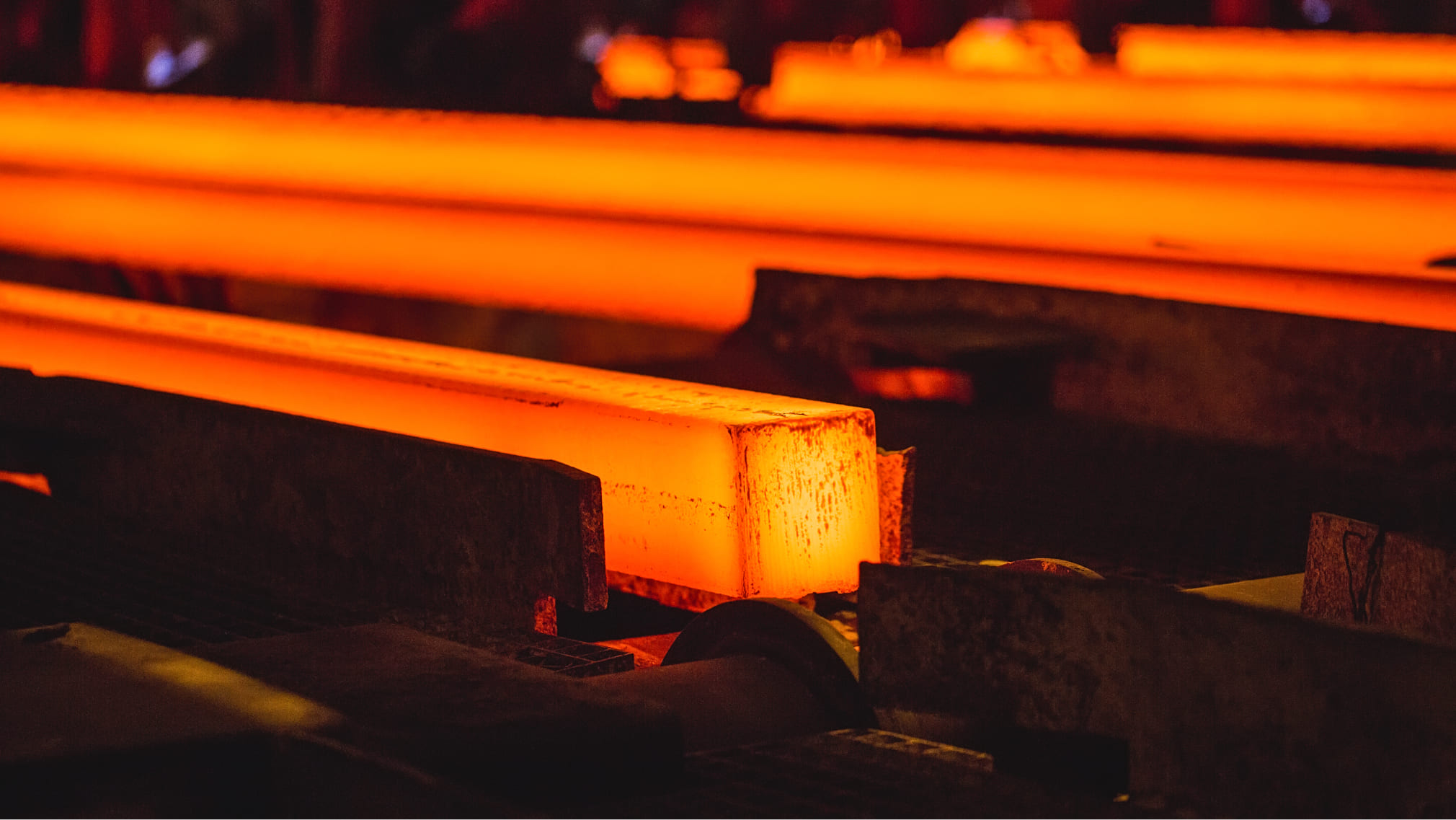
In cosa possiamo aiutare?
Progettiamo
- Calcoli termici con SimuTherm per zone selezionate di forni e siviere
- Progettazione del rivestimento refrattario per siviera torpedo, siviera di ghisa, riscaldatori dell’altoforno, forni spingitori e forni a suola mobile (disegni dei componenti, schede tecniche dei materiali, distinte materiali, istruzioni di montaggio, curve di essiccazione e avviamento, istruzioni di manutenzione)
- Progetti di elementi prefabbricati di rivestimento come: volta del forno elettrico, blocchi bruciatori, blocchi foro di colata, blocchi elettrodo, moduli per murature, volte e suole di forni da laminazione
Produciamo e forniamo
- Ancoraggi ceramici con alta resistenza termica e meccanica, in qualità andalusitica e bauxitica (60–85 % Al₂O₃)
- Elementi prefabbricati di grandi dimensioni quali volte, divisori, blocchi con aperture, blocchi suola
- Sistemi di colata in lingottiera con presse idrauliche e tecnologia semi-secco
- Mattoni isolanti e feltri in fibra ceramica per strati isolanti di forni e siviere
- Checkers in chamotte e alta allumina per recuperatori per altoforno
- Calcestruzzi refrattari (dai convenzionali a ultra low cement), isolanti e miscele per riparazioni a caldo
Installiamo
- Pianificazione e gestione delle manutenzioni, compresi tutti i materiali ausiliari (casseri, componenti metallici, staffe, isolamento in fibra)
- Smontaggio e installazione di rivestimenti ceramici per siviere torpedo, siviere per metallo caldo, recuperatori (cowper) di altoforno e forni per laminatoi
- Consulenza tecnica e supervisione da parte di esperti nel montaggio di rivestimenti ceramici si in muratura che in calcestruzzo
Fours et autres applications à haute température
Forno per la pellettizzazione del minerale di ferro
Il forno per la pellettizzazione consente la sinterizzazione dei pellet precedentemente formati da concentrati di minerale di ferro. Nel forno rotativo, cuore dell’impianto, si distinguono tre zone principali: preriscaldo, cottura e raffreddamento. Per garantire un funzionamento continuo e affidabile, il rivestimento refrattario deve offrire un’elevata resistenza agli shock termici, all’abrasione, nonché alla flessione e compressione (a causa della rotazione del forno e della pressione del carico). PCO propone una gamma di materiali in chamotte e alto allumina in formati standard (ISO, VDZ) o su misura. I forni di pellettizzazione più grandi, per i quali PCO fornisce rivestimenti, hanno un diametro fino a 8 m. Dopo il forno rotativo si trova il raffreddatore per pellet, che può essere rivestito con calcestruzzi, masse da ramming o prefabbricati pronti per l’installazione. I materiali utilizzati in questa zona si distinguono per la loro resistenza agli shock termici e all’abrasione.
Ambito: Progettazione del rivestimento Fornitura dei materiali refrattari Montaggio del rivestimento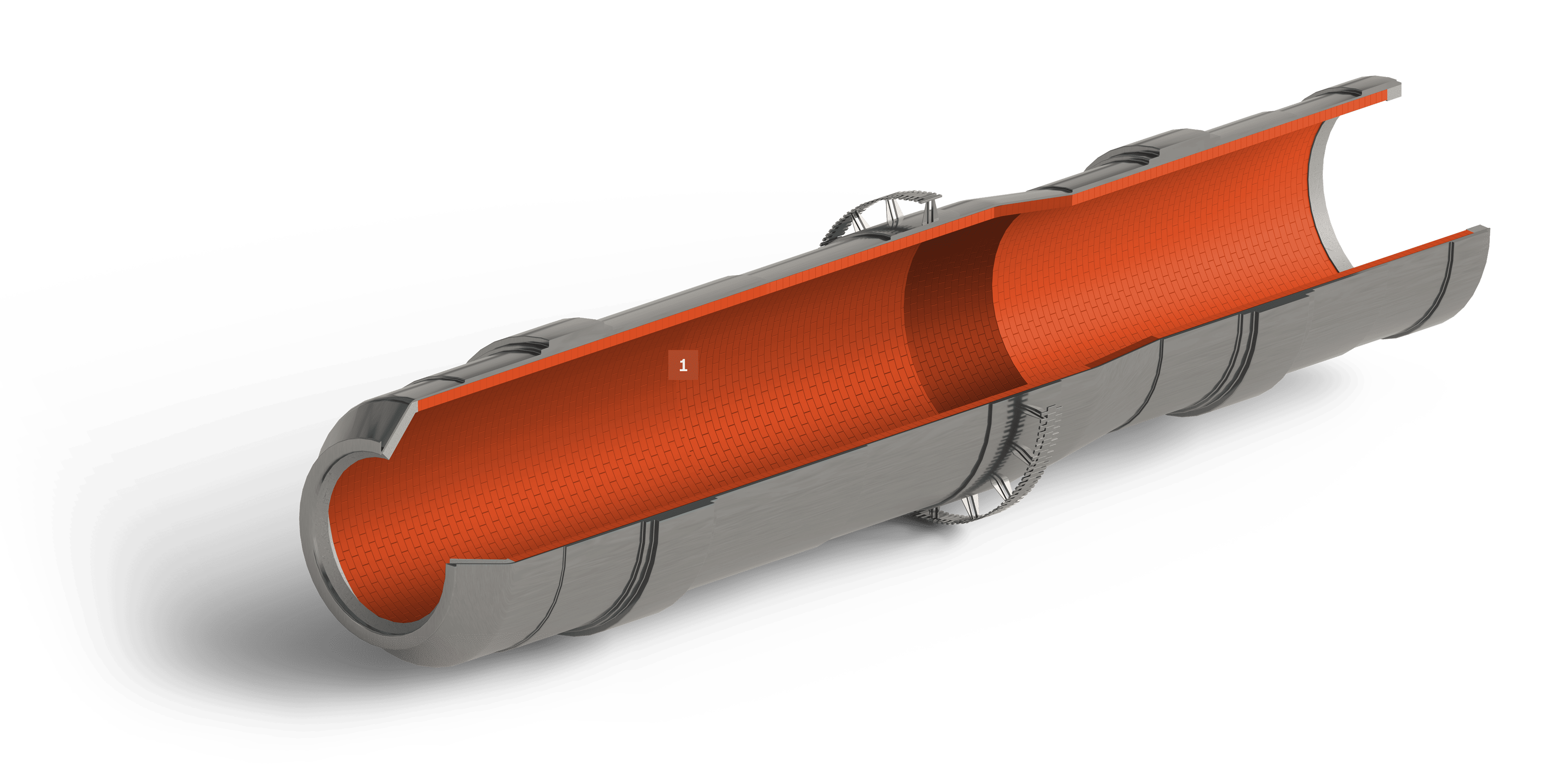
La maggior parte dei forni rotativi per la pellettizzazione utilizza mattoni ad alto contenuto di allumina (60–80 % Al₂O₃). Questa composizione è scelta per la capacità di mantenere un’elevata resistenza meccanica a temperature elevate (fino a 1400 °C nella zona di cottura) e un’eccellente resistenza agli shock termici e all’abrasione. La gestione di questi fattori critici si basa sulla scelta di mattoni progettati con incastri, una posa di alta qualità con malta adeguata e giunti di dilatazione, e, ove possibile, sull’uso di un sistema composito di rivestimento che includa uno strato isolante per ridurre le tensioni termiche.
Come possiamo aiutarti
Se desideri ricevere una consulenza gratuita o porre una domanda sulla scelta del rivestimento refrattario, lasciaci i tuoi dati – ti richiameremo!
ContattaciQuale materiale utilizzare per ridurre la formazione di incrostazioni da polvere o ceneri e minimizzare il distacco di frammenti del rivestimento?
Quale materiale garantisce la resistenza meccanica necessaria per un forno di grande diametro?
Come proteggere il rivestimento dagli effetti dei forti gradienti termici durante il riscaldamento irregolare e il raffreddamento ciclico del forno?
Riscaldatore dell’altoforno
Il riscaldatore dell’altoforno svolge un ruolo fondamentale nella metallurgia, preriscaldando il carico fino a temperature che raggiungono i 1000 °C. Il processo è continuo e la sua efficacia dipende dal controllo preciso del flusso dei gas e dalla distribuzione uniforme del calore. Il rivestimento refrattario è esposto a rapide variazioni di temperatura, alla corrosione chimica dei gas di combustione e all’abrasione da parte delle particelle fini del carico, il che richiede l’impiego di materiali altamente resistenti. Negli strati superiori vengono utilizzate griglie in silice, caratterizzate da resistenza alla deformazione termica e stabilità chimica. Nelle sezioni inferiori si impiegano prodotti in chamotte, resistenti alle alte temperature e agli intensi carichi meccanici, mentre gli elementi in andalusite usati nelle zone superiori garantiscono stabilità dimensionale e resistenza agli agenti chimici. Inoltre, gli strati isolanti realizzati con mattoni prodotti da PCO riducono efficacemente le perdite di calore, aumentando l’efficienza energetica dell’intero sistema e assicurando affidabilità e durata anche in condizioni industriali estreme.
Ambito: Progettazione del rivestimento Fornitura dei materiali refrattari Montaggio del rivestimento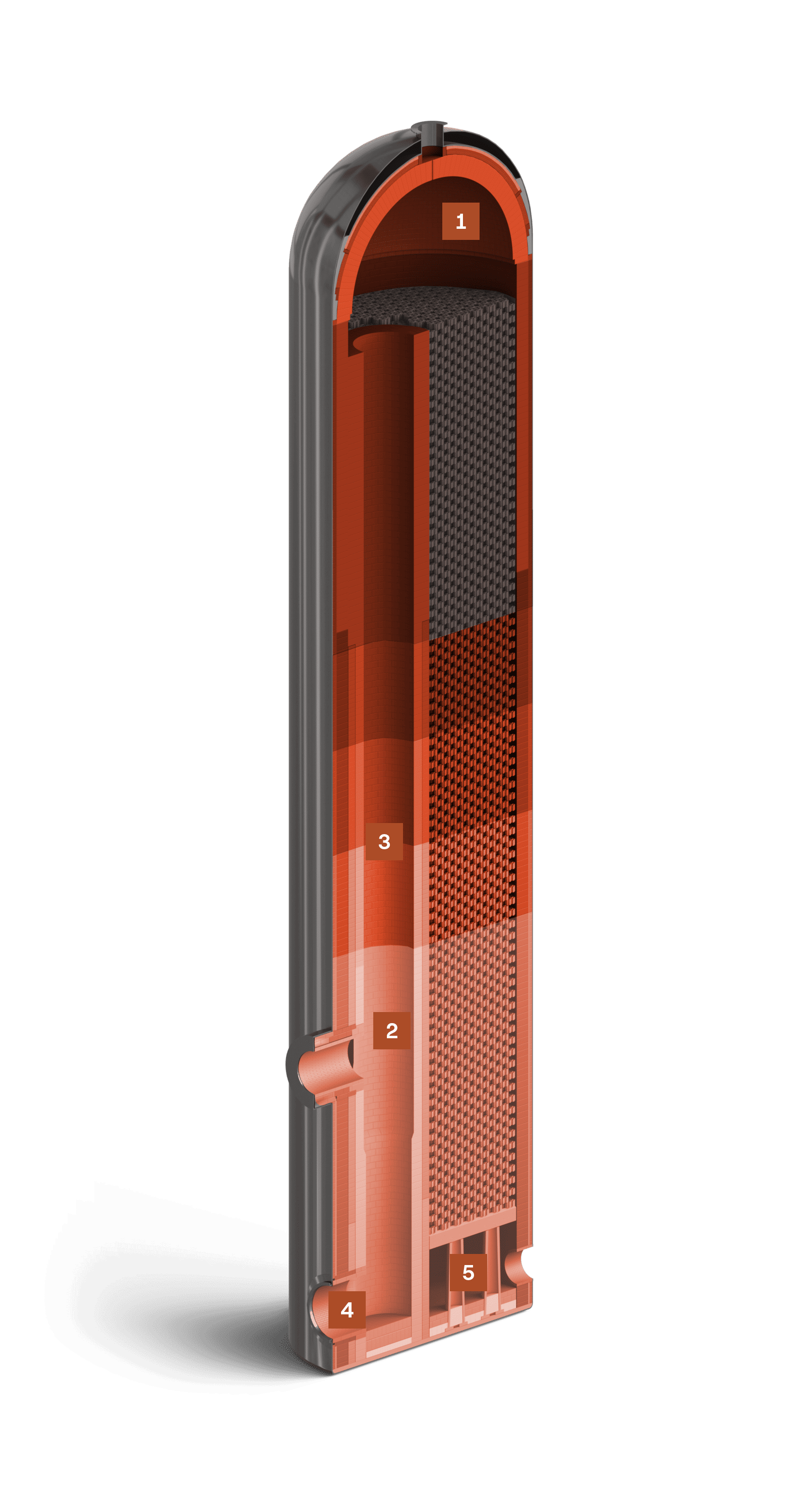
Nella cupola del riscaldatore, dove la temperatura raggiunge i 1300–1400 °C, i materiali refrattari devono resistere ad atmosfere ossidanti e riducenti, a forti carichi meccanici e a rapidi cambiamenti di temperatura che provocano shock termici e degrado strutturale. La durabilità del rivestimento è assicurata dall’uso di materiali con elevato grado di mullitizzazione, come i prodotti ANDALUX, che offrono stabilità dimensionale, bassa porosità e resistenza alla corrosione. La scelta accurata dei materiali è fondamentale per l’affidabilità del sistema e l’efficienza del processo.
In questa zona del riscaldatore, i materiali refrattari devono resistere a temperature estreme, ambienti chimicamente aggressivi e intensi shock termici. Sono fondamentali i prodotti ad alto contenuto di mullite come ANDALUX, che garantiscono stabilità anche sotto carichi termici estremi. Nelle zone a temperatura leggermente inferiore si utilizzano prodotti SUPERTON, che grazie alla loro resistenza meccanica assicurano la durabilità del rivestimento. Inoltre, i materiali ISOLUX limitano le perdite di calore, aumentando l’efficienza energetica e prolungando la vita operativa del riscaldatore.
Le griglie nella zona del rigeneratore svolgono un ruolo chiave nello scambio termico, permettendo un riscaldamento efficiente dell’aria diretta all’altoforno. I materiali impiegati in questa sezione devono avere un’eccellente resistenza alle alte temperature, ai gas aggressivi e ai carichi meccanici. A seconda della zona, si utilizzano elementi grigliati in chamotte o andalusite, che garantiscono stabilità strutturale e durata nel tempo.
I bruciatori forniscono energia termica al sistema del riscaldatore, per cui è essenziale selezionare accuratamente i materiali refrattari. Questi devono garantire lunga durata, alta efficienza energetica e sicurezza del processo. In condizioni di esercizio dinamiche, si utilizzano prevalentemente materiali refrattari a base di mullite, che combinano resistenza agli shock termici con la capacità di mantenere temperature elevate. Una corretta selezione di questi materiali riduce il rischio di degrado, migliorando l’affidabilità del sistema.
I condotti trasportano aria caldissima dal riscaldatore all’altoforno. Operano ad alte temperature, in condizioni chimiche aggressive e con variazioni termiche dinamiche, per cui è fondamentale scegliere materiali refrattari resistenti. Nelle zone a temperatura moderata si impiega chamotte, apprezzata per la convenienza economica, mentre in zone soggette a forti variazioni termiche si usano materiali in mullite, che assicurano stabilità e affidabilità del sistema.
Come possiamo aiutarti
Se desideri ricevere una consulenza gratuita o porre una domanda sulla scelta del rivestimento refrattario, lasciaci i tuoi dati – ti richiameremo!
ContattaciCome progettare le griglie per minimizzare le incrostazioni e la formazione di scorie nel rigeneratore?
Quale materiale proteggerà meglio i bruciatori contro lo spalling e gli shock termici?
Come realizzare i giunti di dilatazione nei rivestimenti ceramici per compensare i cambiamenti dimensionali causati da riscaldamento e raffreddamento?
Siviera torpedo
La siviera torpedo, utilizzata per il trasporto dell’acciaio liquido dal convertitore alle postazioni di colata, deve resistere a condizioni termiche estreme, con temperature che spesso superano i 1600 °C. Queste unità hanno una grande capacità — da circa 200 fino a 460 tonnellate — e operano in cicli rapidi di riempimento, trasporto e svuotamento, che generano forti variazioni di temperatura e sollecitazioni meccaniche dinamiche. Il rivestimento refrattario della siviera torpedo è progettato per minimizzare la perdita di calore, resistere agli shock termici e contrastare l’azione aggressiva dei composti chimici presenti nell’acciaio liquido. Particolare attenzione viene riservata all’erosione causata dal metallo caldo e dalla scoria. PCO Żarów offre una gamma completa di materiali refrattari per la costruzione delle siviere torpedo, inclusi prodotti per gli strati protettivi e di lavoro. L’offerta comprende calcestruzzi refrattari e prefabbricati utilizzati nelle aree più critiche, come la gola e la zona d’impatto.
Ambito: Progettazione del rivestimento Fornitura dei materiali refrattari Montaggio del rivestimento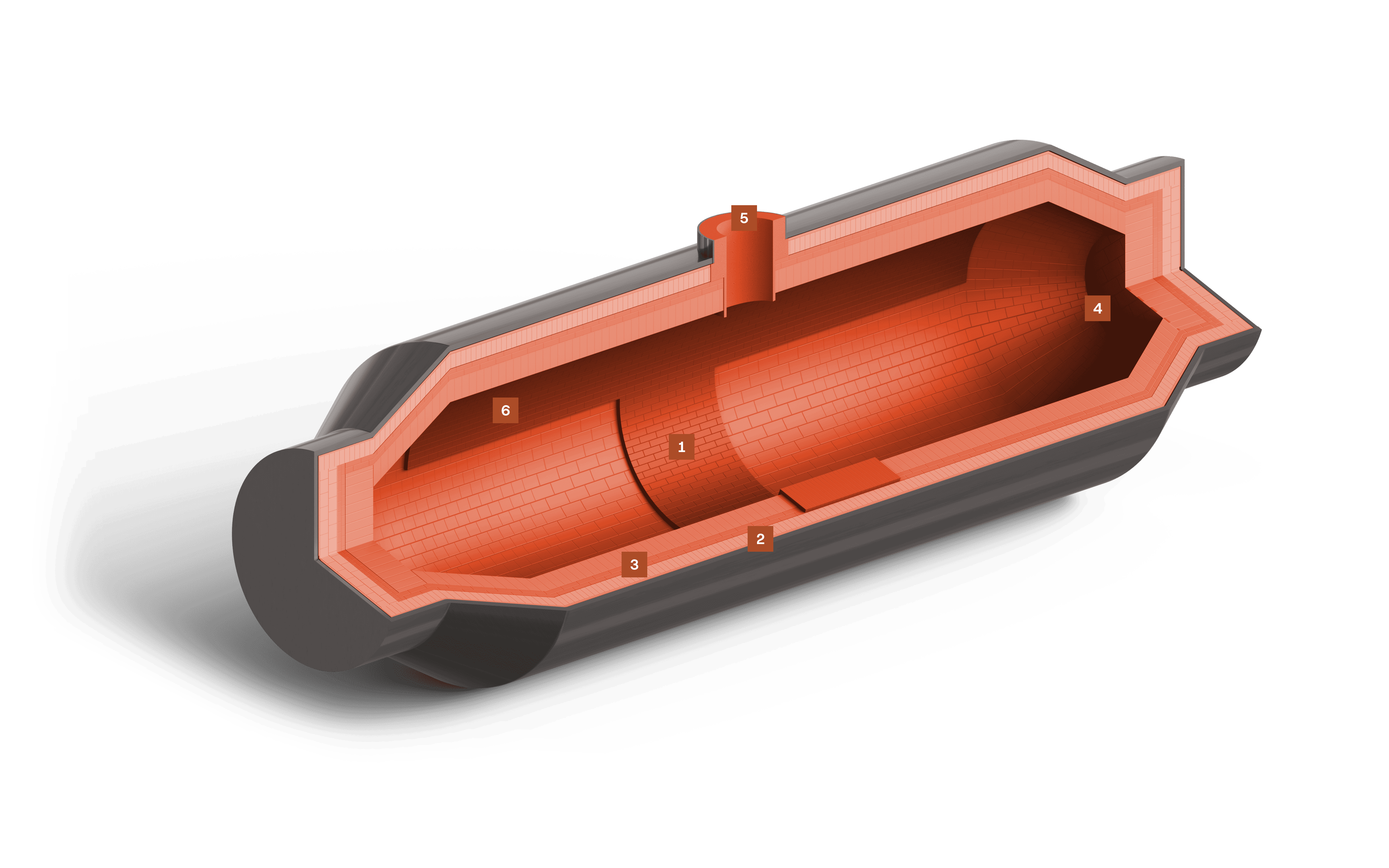
È la zona in cui l’acciaio liquido colpisce violentemente il rivestimento, generando shock termici e meccanici estremi. I materiali refrattari in questa area devono offrire altissima resistenza termica e capacità di assorbire impulsi termici intensi senza compromettere la struttura. È fondamentale mantenere la continuità del rivestimento anche sotto forti impatti, per evitare la degradazione. I prodotti impiegati garantiscono stabilità strutturale anche nelle condizioni più estreme, essenziali per un funzionamento affidabile e duraturo.
Lo strato isolante protegge la struttura della siviera da perdite di calore e deformazioni dovute al trasporto di grandi volumi di metallo caldo. Di norma, si utilizza un sistema multistrato composto da mattoni o pannelli refrattari isolanti, abbinati a materassini in lana minerale. Questo sistema forma una barriera termica e meccanica compatta, riducendo il rischio di deformazioni. I materiali PERLITEX e ISOLUX offerti da PCO soddisfano questi requisiti, assicurando isolamento efficace e affidabilità durante il trasporto della ghisa.
Lo strato protettivo, come quello di transizione, ha il compito di proteggere il rivestimento dal contatto diretto con acciaio liquido e scoria, che causano forte abrasione e attacco chimico. In caso di cedimento dello strato di lavoro, lo strato protettivo deve garantire la protezione della struttura. Vengono utilizzati mattoni della serie NORMATON, SUPERTON e ANDALUX, talvolta anche come strato intermedio. Il materiale deve offrire alta capacità isolante, resistenza all’usura e alla compressione, oltre a tollerare il contatto con metallo e scoria.
È lo strato a diretto contatto con l’acciaio liquido e il più esposto a condizioni di processo aggressive e azioni erosive. Gli shock termici estremi e l’azione corrosiva richiedono materiali di altissima resistenza e precisione dimensionale. Le siviere torpedo, per la loro geometria e anni di utilizzo, possono deformarsi: per questo è essenziale che i materiali dello strato di lavoro abbiano tolleranze molto ristrette. In alcuni casi, dietro lo strato di lavoro si applica uno strato di transizione compatibile con lo strato protettivo, garantendo la stabilità dell’intera struttura.
Attraverso la gola viene colato e scaricato l’acciaio liquido. A causa della sua geometria complessa e dell’intensità delle sollecitazioni, si utilizzano calcestruzzi refrattari densi che formano una struttura solida e omogenea, resistente ai flussi violenti del metallo. PCO Żarów propone calcestruzzi ad alte prestazioni con elevata resistenza termica ed erosiva. Tra le soluzioni consigliate vi sono calcestruzzi “fast dry”, che si asciugano rapidamente a basse temperature — un grande vantaggio rispetto ai calcestruzzi convenzionali.
È la parte dove si accumulano scorie e ceneri residue. Sebbene le temperature siano più miti, l’aumento dell’attrito crea ulteriori sollecitazioni meccaniche, che possono innescare reazioni secondarie. I materiali in questa zona devono offrire alta resistenza all’usura e all’abrasione per proteggere a lungo la struttura. I prodotti selezionati devono garantire resistenza anche a basse temperature e in presenza di attrito, assicurando stabilità e durabilità del rivestimento.
Come possiamo aiutarti
Se desideri ricevere una consulenza gratuita o porre una domanda sulla scelta del rivestimento refrattario, lasciaci i tuoi dati – ti richiameremo!
ContattaciCorrosione del rivestimento nella zona scoria: quale materiale resiste meglio alla scoria d’altoforno?
Quale configurazione multistrato protegge al meglio il rivestimento dagli shock termici durante i cicli di riempimento?
Come scegliere il materiale per minimizzare l’erosione del rivestimento nella zona d’impatto?
Siviera di ghisa
La siviera di ghisa, utilizzata nei processi di produzione del ferro, svolge un ruolo essenziale come contenitore per il trasporto e lo stoccaggio della ghisa fusa a temperature comprese tra 1400 e 1500 °C. Il processo di trasporto, operato in modo continuo o ciclico, richiede un controllo preciso dei parametri termici e meccanici per garantire la qualità e la composizione chimica del metallo. Il rivestimento refrattario della siviera deve sopportare carichi termici elevati, shock termici durante il riempimento e lo svuotamento, l’azione di gas di combustione aggressivi e la presenza di scorie. È fondamentale scegliere miscele refrattarie con alta resistenza alla corrosione e all’abrasione, per assicurare un funzionamento duraturo anche in condizioni operative difficili. PCO Żarów offre rivestimenti completi per siviere da ghisa liquida, che comprendono sia gli strati protettivi che quelli di lavoro. Nelle zone di contatto con la ghisa liquida si utilizzano speciali mattoni refrattari, mentre i bordi della siviera sono protetti da calcestruzzi refrattari. Per lo strato isolante vengono proposti mattoni isolanti e calcestruzzi isolanti leggeri, che garantiscono un isolamento termico efficace e minimizzano le perdite di calore.
Ambito: Progettazione del rivestimento Fornitura dei materiali refrattari Montaggio del rivestimento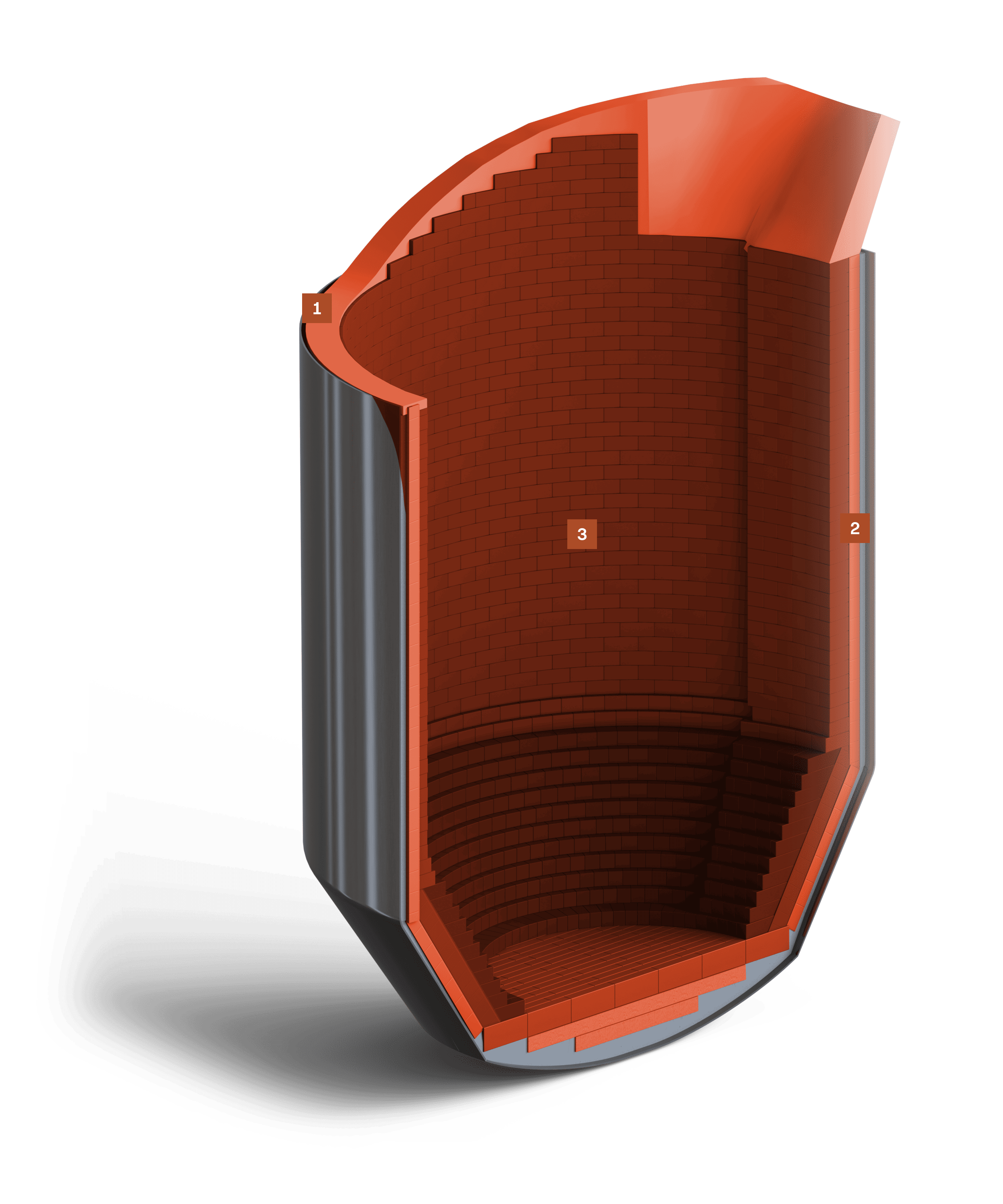
In questa zona il materiale deve offrire non solo elevata refrattarietà, ma anche resistenza alla corrosione ed erosione causate dall’acciaio liquido e dalla scoria. L’intensità del lavoro e i possibili impatti meccanici durante il trasporto sollecitano ulteriormente la struttura. PCO Żarów propone calcestruzzi refrattari a basso o medio contenuto di cemento, applicabili sia per colata che per spruzzatura. Il materiale usato per il bordo è lo stesso impiegato per il becco di colata, semplificando la costruzione della siviera.
Questo strato svolge una funzione fondamentale nel ridurre la perdita di calore, consentendo di mantenere la temperatura ottimale della ghisa. PCO Żarów propone soluzioni complete che combinano mattoni refrattari densi e calcestruzzi specializzati. I materiali selezionati sono altamente resistenti alle temperature estreme e agli ambienti operativi aggressivi, garantendo una lunga durata della siviera. La scelta corretta dei materiali isolanti permette di adattare perfettamente le prestazioni del rivestimento alle specifiche esigenze del processo, ottimizzando i costi operativi.
Il rivestimento ceramico di lavoro della siviera è soggetto a deformazioni, per cui è essenziale fornire forme refrattarie con tolleranze dimensionali molto strette. È altrettanto importante che l’espansione termica dei materiali sia controllata per evitare il degrado delle giunzioni dovuto ai cicli termici. I materiali devono resistere a condizioni estreme: alte temperature, forti shock termici e l’azione aggressiva di metallo fuso e scorie. Una selezione corretta assicura resistenza a corrosione ed erosione, nonché stabilità strutturale, indispensabile per il controllo del processo e la qualità del prodotto finale.
Come possiamo aiutarti
Se desideri ricevere una consulenza gratuita o porre una domanda sulla scelta del rivestimento refrattario, lasciaci i tuoi dati – ti richiameremo!
ContattaciCome proteggere il rivestimento alluminosilicatico dagli effetti aggressivi della scoria basica?
Quale configurazione multistrato minimizza le fessurazioni termo-meccaniche dello strato di lavoro?
Quale calcestruzzo refrattario offre la miglior resistenza all’erosione da flusso nella zona del bordo e del becco?
Miscelatore di ghisa
Il miscelatore di ghisa viene utilizzato per lo stoccaggio (buffer) e l’omogeneizzazione della ghisa d’altoforno presso l’acciaieria, mantenendo le sue proprietà desiderate – in particolare la temperatura. Il rivestimento refrattario del miscelatore opera a temperature estremamente elevate, intorno ai 1400–1500 °C, e deve resistere a forti variazioni termiche, corrosione chimica ed erosione causata dal flusso di metallo liquido. La scelta dei materiali refrattari dipende dalla zona del miscelatore, in quanto ogni area è soggetta a carichi diversi. I prodotti PCO sono impiegati sia nello strato di lavoro della zona superiore, sia negli strati isolanti al di sotto del rivestimento principale, garantendo una protezione ottimale e una lunga durata dell’impianto. PCO Żarów fornisce anche rivestimenti colati per i blocchi bruciatore e la punta del miscelatore. Per la zona cilindrica superiore, che non è a contatto diretto con il metallo, forniamo mattoni andalusitici ad alto contenuto di allumina.
Ambito: Progettazione del rivestimento Fornitura dei materiali refrattari Montaggio del rivestimento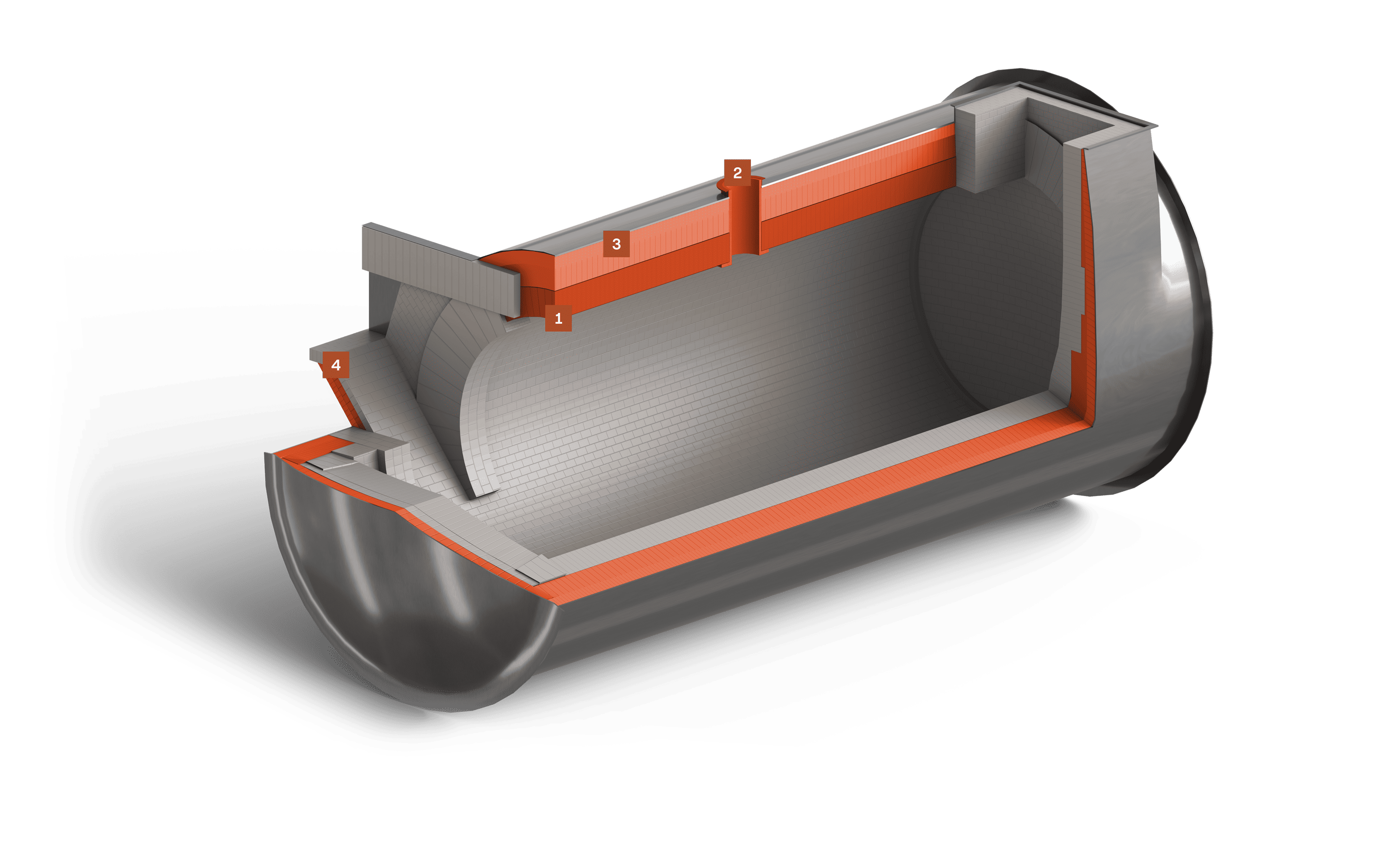
Questa zona include la parte superiore della camera cilindrica, le pareti laterali e l’apertura di carico. Il rivestimento è soggetto a shock termici intensi e a erosione provocata dal flusso dell’acciaio liquido. I prodotti ANDALUX ad alto contenuto di allumina e a base alluminosilicatica offrono eccellente resistenza agli shock termici e all’erosione, mantenendo le proprie caratteristiche anche in presenza di metallo fuso.
In questa zona, i materiali refrattari sono esposti a usura meccanica intensiva e attacchi chimici aggressivi. Per soddisfare tali esigenze, PCO Żarów propone il calcestruzzo PCOCAST BN X222, a basso contenuto di cemento, che mantiene elevate prestazioni a temperature fino a 1600 °C.
L’obiettivo principale dello strato isolante è ridurre al minimo le perdite di calore e proteggere la struttura metallica del miscelatore dal surriscaldamento. Si impiegano sia prodotti chamotte con contenuto di Al₂O₃ del 42–44% (es. SUPERTON), sia materiali isolanti leggeri della serie ISOLUX. Questa combinazione garantisce ottimo isolamento termico, resistenza alla compressione e stabilità termica.
La punta del miscelatore è soggetta a temperature elevate, shock termici violenti e usura meccanica e chimica, come nel caso del bruciatore. È fondamentale la resistenza al contatto diretto con l’acciaio liquido e la scoria. PCO Żarów consiglia il calcestruzzo PCOCAST BN X222, che conserva le proprie caratteristiche fino a 1600 °C.
Come possiamo aiutarti
Se desideri ricevere una consulenza gratuita o porre una domanda sulla scelta del rivestimento refrattario, lasciaci i tuoi dati – ti richiameremo!
ContattaciQuale materiale per gli strati protettivi sopporta meglio le tensioni termiche durante i cicli di esercizio?
Quali materiali resistono a deformazioni e creep causati da carichi meccanici durante la rotazione del miscelatore?
Come integrare un rivestimento alluminosilicatico con uno basico nella zona metallica superiore?
Volta del forno elettrico (EAF)
La volta dell’EAF costituisce la parte interna, a cupola, che circonda direttamente la zona dell’arco elettrico, dove si generano temperature estremamente elevate, superiori ai 1600 °C. La sua funzione principale è non solo proteggere la struttura del forno, ma anche garantire una distribuzione uniforme del calore e ridurre le perdite termiche durante i cicli di lavoro intensi. La carica nel forno è esposta all'azione dell'arco elettrico e la corrente dagli elettrodi fluisce direttamente attraverso il materiale di carica. L’usura del rivestimento refrattario in un forno EAF è significativamente più rapida rispetto ad altri impianti termici nella produzione dell’acciaio.
Ambito: Progettazione del rivestimento Fornitura dei materiali refrattari Montaggio del rivestimento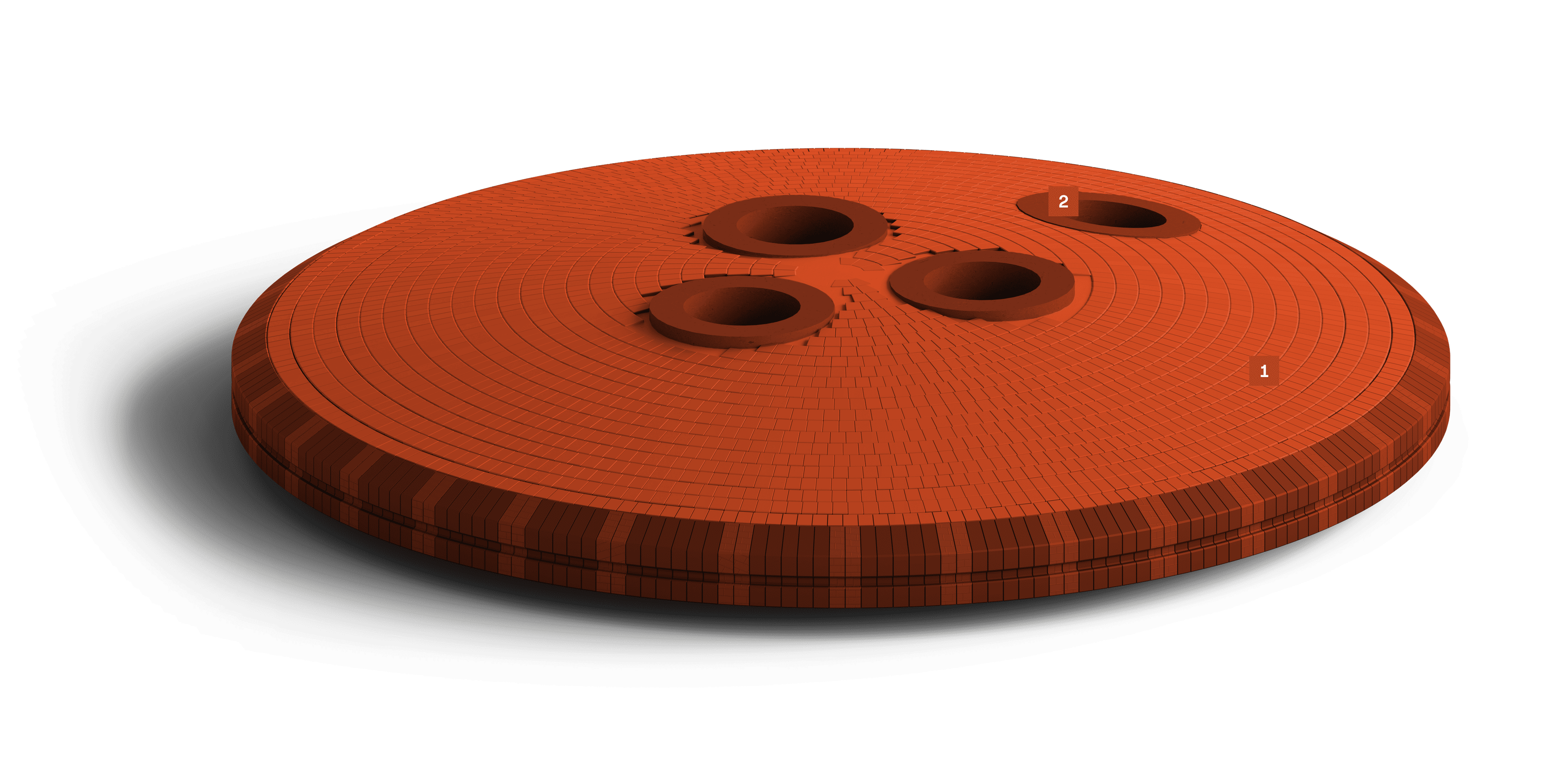
Per prolungare la vita utile di questo componente critico, abbiamo sviluppato speciali calcestruzzi refrattari della serie PCOCAST, come 170KCR5 e BNX222. Grazie a tecnologie avanzate, questi calcestruzzi sono altamente resistenti alle rapide variazioni di temperatura, garantendo la stabilità strutturale della volta. Un ulteriore vantaggio è il tempo di presa ottimizzato, che consente il getto e l’essiccazione direttamente in acciaieria (“sul ragno”) o presso il nostro stabilimento.
I blocchi per elettrodi sono gli elementi che circondano le aperture attraverso le quali gli elettrodi di grafite vengono introdotti nel forno. Grazie a questi blocchi, gli elettrodi possono muoversi in modo sicuro (sollevarsi e abbassarsi) durante il funzionamento del forno, e l'arco elettrico stesso viene mantenuto nella posizione corretta all'interno della camera di fusione. Per questi blocchi consigliamo mattoni ad alto tenore di allumina e calcestruzzi a basso contenuto di cemento con un contenuto di Al2O3 superiore all'80%.
Come possiamo aiutarti
Se desideri ricevere una consulenza gratuita o porre una domanda sulla scelta del rivestimento refrattario, lasciaci i tuoi dati – ti richiameremo!
ContattaciCome progettare la volta per ottenere la massima resistenza a rapidi aumenti di temperatura e prevenire il distacco del rivestimento?
Quale materiale garantisce resistenza alla corrosione da vapori condensabili sulla volta?
Come progettare e murare le forme intorno agli elettrodi per evitare fessurazioni dovute a vibrazioni e movimento degli elettrodi?
Siviera principale (acciaieria)
La siviera principale, utilizzata per il trasporto dell’acciaio liquido durante la fusione e le fasi successive di lavorazione, opera a temperature comprese tra 1550 e 1650 °C e affronta cicli termici molto intensi. La sua funzione principale è mantenere la stabilità del metallo trasportato riducendo al minimo la perdita di calore — condizione essenziale per preservare i parametri chimici ottimali dell’acciaio. Il rivestimento refrattario della siviera deve resistere a rapide variazioni di temperatura, sollecitazioni meccaniche e corrosione chimica causata dai componenti metallici fusi e dai prodotti della combustione. PCO Żarów fornisce prodotti refrattari dedicati al guscio e agli strati protettivi delle pareti, utilizzando mattoni magnesiaci nello strato di lavoro. Il rivestimento del fondo della siviera, inclusi lo strato di lavoro e le forme di colata, può essere realizzato con prodotti alluminosilicatici non cotti, che garantiscono stabilità e durata anche in condizioni operative estreme.
Ambito: Progettazione del rivestimento Fornitura dei materiali refrattari Montaggio del rivestimento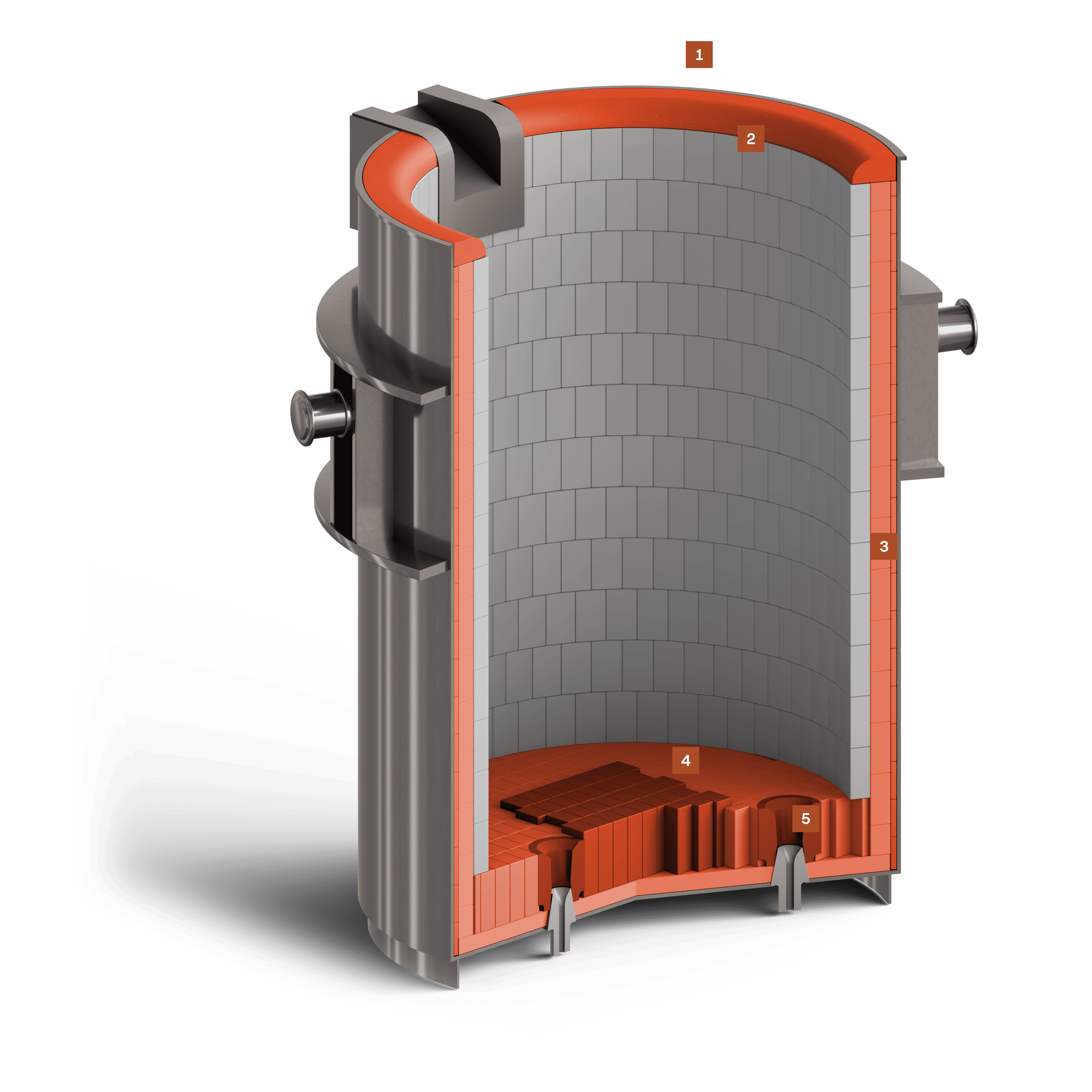
Il coperchio della siviera è responsabile della conservazione della temperatura dell’acciaio durante il trasporto. Deve pertanto offrire sia alta resistenza termica sia eccellente isolamento. PCO Żarów ha sviluppato un calcestruzzo speciale che, pur mantenendo un’alta resistenza al calore, offre una maggiore capacità isolante rispetto ai calcestruzzi standard della stessa categoria. Questo consente di mantenere la temperatura ottimale, riducendo al tempo stesso il peso del coperchio e il consumo di materiale.
Il bordo della siviera è esposto all’azione dell’acciaio liquido, della scoria e a urti meccanici durante il trasporto. I materiali refrattari utilizzati in questa zona devono unire resistenza alle alte temperature, agli attacchi chimici e ai carichi meccanici dinamici. PCO Żarów propone diverse formulazioni di calcestruzzi refrattari — a basso contenuto di cemento, ultra low cement o senza cemento — prodotti con aggregati di alta qualità.
Lo strato protettivo ha un ruolo cruciale nella riduzione delle perdite di calore, contribuendo al mantenimento della temperatura dell’acciaio. Un buon isolamento interno riduce le perdite termiche, aumentando l’efficienza della colata e riducendo i costi energetici. PCO Żarów propone sia mattoni refrattari densi sia calcestruzzi refrattari per questo strato, assicurando alte prestazioni isolanti e resistenza alle sollecitazioni meccaniche dinamiche.
È la zona a contatto diretto con acciaio fuso e scorie. Qui è fondamentale mantenere l’integrità e la continuità del rivestimento ceramico. Per questa zona PCO Żarów ha sviluppato un prodotto chimicamente legato dedicato all’area di impatto. Per le pareti della zona metallo e scoria vengono impiegati prodotti delle serie ANDALUX e BAUXITEX, che garantiscono alta resistenza alla corrosione e contribuiscono alla durata del rivestimento.
Le forme di colata guidano il flusso dell’acciaio fuso e sono tra i componenti più critici. I materiali impiegati devono avere purezza elevata e stabilità chimica e termica. PCO Żarów ha sviluppato diversi calcestruzzi legati a spinello specifici per queste forme, con eccezionale resistenza alla corrosione e all’erosione da acciaio liquido, riducendo al minimo i rischi di degrado anche dopo uso prolungato.
Come possiamo aiutarti
Se desideri ricevere una consulenza gratuita o porre una domanda sulla scelta del rivestimento refrattario, lasciaci i tuoi dati – ti richiameremo!
ContattaciErosione del fondo della siviera: come progettare il “tappeto d’impatto” e ridurre l’usura delle forme di colata?
Quali prodotti proteggono meglio lo strato protettivo da fessurazioni e distacchi causati da shock termici?
Come valutare la necessità di una revisione del rivestimento in base all’usura della ceramica nella zona scoria?
Siviera intermedia (tundish)
La siviera intermedia (tundish) svolge un ruolo fondamentale nel processo di colata continua dell’acciaio. Le sue funzioni principali sono il contenimento temporaneo e la distribuzione del metallo liquido, assicurando la continuità del processo durante il cambio della siviera principale. Inoltre, il rivestimento interno è progettato per favorire l’omogeneizzazione della temperatura e della composizione chimica dell’acciaio. Il rivestimento refrattario deve garantire elevata resistenza agli shock termici, all’erosione chimica intensa causata dal metallo liquido e all’abrasione provocata dal suo flusso. Il controllo preciso dei parametri di processo e la scelta corretta dei materiali refrattari sono fondamentali per la stabilità operativa della siviera. PCO Żarów fornisce tutti i componenti necessari per lo strato di lavoro: rivestimento del coperchio, paratie prefabbricate, piastre sottogetto e forme di colata per le zone di scarico del metallo.
Ambito: Progettazione del rivestimento Fornitura dei materiali refrattari Montaggio del rivestimento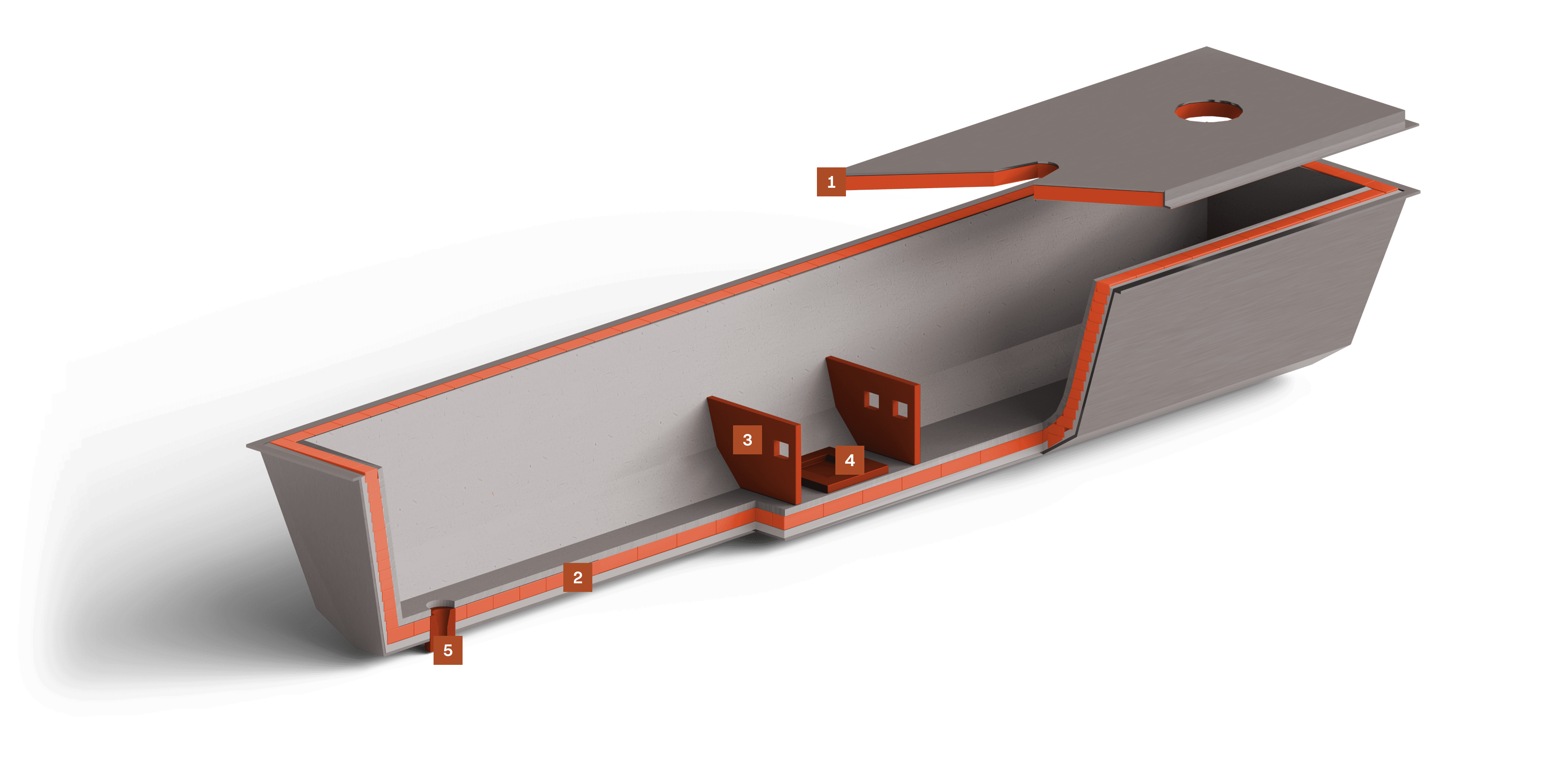
Il coperchio è responsabile della conservazione della temperatura dell’acciaio riducendo le perdite di calore. PCO Żarów propone calcestruzzi ad alto contenuto di allumina che, oltre all’elevata resistenza termica, offrono anche eccellenti proprietà isolanti. Questo consente di mantenere la temperatura del metallo, ridurre la massa del rivestimento e ottimizzare i costi operativi.
Serve principalmente a ridurre la dispersione termica. Le soluzioni PCO includono mattoni isolanti (es. ISOLUX) con elevato potere isolante e mattoni densi come ANDALUX e BAUXITEX, resistenti a sollecitazioni meccaniche e attacchi chimici in caso di penetrazione attraverso lo strato di lavoro. I calcestruzzi PCOCAST e MULCAST, con ottima scorrevolezza, garantiscono un riempimento omogeneo e senza vuoti, migliorando l’efficienza isolante.
Le paratie servono a eliminare le turbolenze durante il riempimento, riducendo le inclusioni e migliorando l’omogeneità dell’acciaio. In questa zona il rivestimento è soggetto ad attacchi erosivi e corrosivi da parte dell’acciaio fuso e della scoria. I prodotti PCO offrono elevata refrattarietà e resistenza agli agenti aggressivi, garantendo lunga durata e affidabilità.
Queste piastre proteggono la tundish dalla perforazione da parte dell’acciaio. Devono essere realizzate con grande precisione, offrendo struttura uniforme e resistenza a shock termici e meccanici. PCO Żarów fornisce piastre sia pressate a secco sia colate in calcestruzzo, già testate con successo in condizioni operative industriali.
Essendo a contatto diretto con l’acciaio liquido, queste forme devono presentare eccellente resistenza termica, agli shock, minimo ritiro e massima precisione di fabbricazione per garantire la tenuta del foro di colata. PCO Żarów offre una vasta gamma di prodotti pressati (es. ANDALUX, BAUXITEX) e prefabbricati (PCOCAST, MULCAST), per prestazioni affidabili anche nelle condizioni più critiche.
Come possiamo aiutarti
Se desideri ricevere una consulenza gratuita o porre una domanda sulla scelta del rivestimento refrattario, lasciaci i tuoi dati – ti richiameremo!
ContattaciQuale rivestimento di lavoro resiste meglio allo shock termico durante il primo colaggio?
Come progettare le paratie per resistere all’abrasione, corrosione e lavaggio del materiale?
Quale materiale scegliere per evitare contaminazioni del metallo da inclusioni ceramiche?
Colata in sorgente
Il sistema di colata in sorgente, parte integrante delle linee di colata in lingotti, è composto da una serie di elementi ceramici che consentono la distribuzione precisa del metallo fuso negli stampi. Questi componenti operano a temperature molto elevate (spesso superiori a 1600 °C) e sono sottoposti a rapide variazioni di flusso e pressione. I materiali refrattari utilizzati nel set ceramico devono essere resistenti a intensi carichi termici, a cicli rapidi di riscaldamento e raffreddamento, nonché alla corrosione chimica causata dall'ambiente aggressivo del metallo fuso. Di importanza cruciale è la superficie di contatto del metallo liquido con gli elementi ceramici, che non deve rilasciare impurità (inclusioni) e deve garantire una facile separazione dal metallo al termine del processo di colata. L'adeguamento preciso delle soluzioni materiali alle condizioni di processo, e in particolare al tipo di acciaio colato, consente di mantenere parametri tecnologici ottimali e garantisce un'elevata qualità dei getti.
Ambito: Progettazione del rivestimento Fornitura dei materiali refrattari Montaggio del rivestimento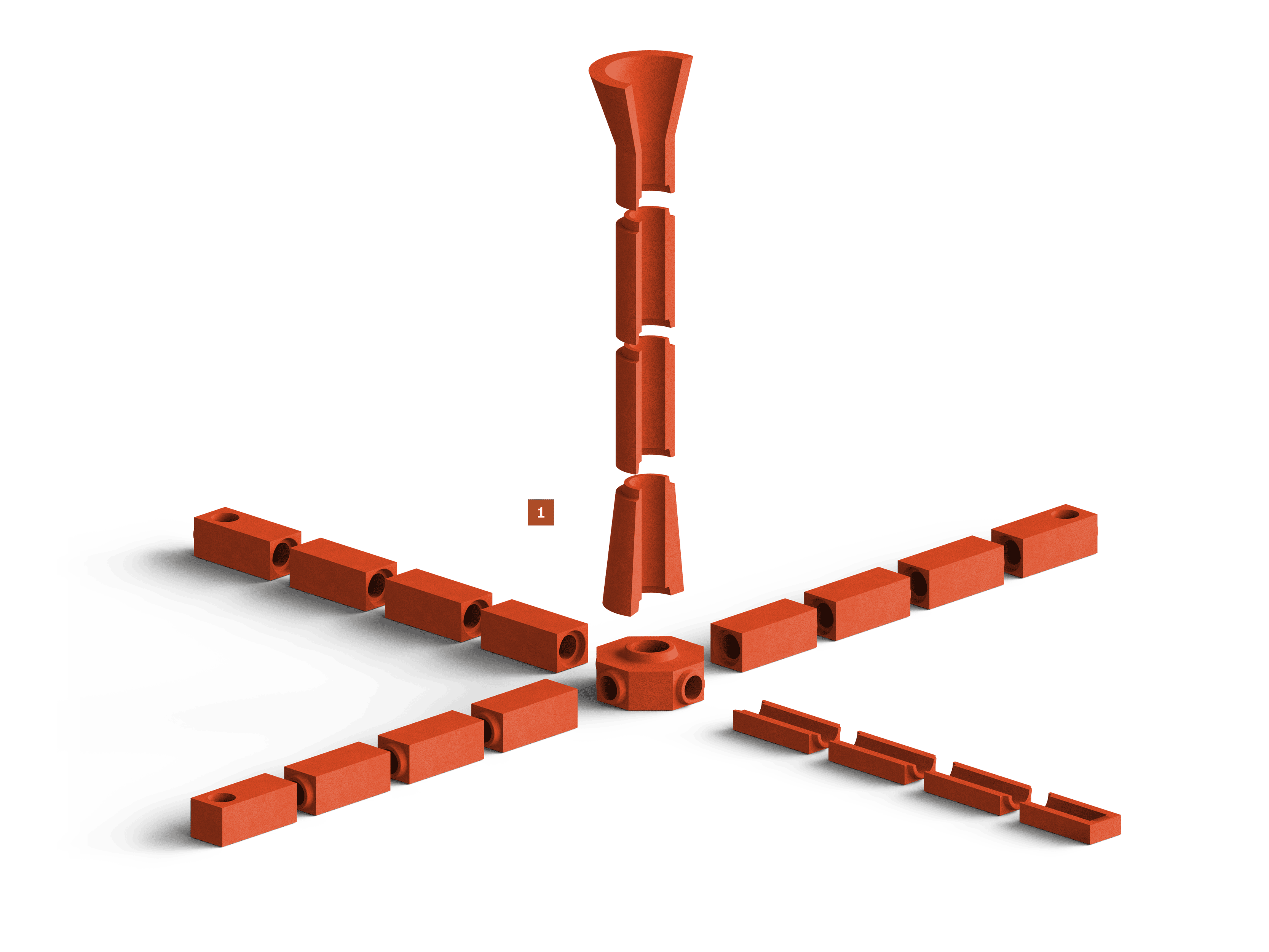
PCO fornisce sistemi completi di colata a sifone con varie capacità. Grazie al metodo di produzione (pressatura di massa semisecca), gli spessori minimi delle pareti dei nostri componenti raggiungono i 20 mm. La produzione con pressatura a secco garantisce elevata precisione nei dettagli di incastri, canaline, fori e piastre distributrici, assicurando perfetta compatibilità tra gli elementi del sistema.
Come possiamo aiutarti
Se desideri ricevere una consulenza gratuita o porre una domanda sulla scelta del rivestimento refrattario, lasciaci i tuoi dati – ti richiameremo!
ContattaciQuale materiale offre la massima resistenza allo shock termico durante la colata?
Come progettare le dimensioni degli elementi per ridurre il rischio di erosione e abrasione di tubi e canali?
Quale materiale minimizza l’interazione con l’acciaio e previene la formazione di inclusioni indesiderate?
Forno a spinta
Il forno a spinta viene utilizzato per il riscaldamento dell’acciaio prima della deformazione plastica, come la laminazione o la forgiatura. Questi forni sono suddivisi in zone funzionali: preriscaldo, riscaldamento e omogeneizzazione. Per garantire un funzionamento efficiente e duraturo, è fondamentale impiegare materiali refrattari con elevata resistenza all’erosione, all’abrasione e agli shock termici. Nella zona di lavoro del forno, dove il metallo è a contatto diretto con il rivestimento, si utilizzano calcestruzzi refrattari o elementi prefabbricati con alta resistenza meccanica e agli shock termici. Nelle aree meno sollecitate direttamente dal metallo caldo, si possono usare calcestruzzi refrattari, masse da ramming o forme sagomate, che offrono ottime proprietà isolanti e buona resistenza meccanica. I sistemi multistrato, composti da strati di lavoro e strati isolanti, consentono di ottenere le migliori prestazioni termiche, migliorando l’efficienza del processo e la durata del forno.
Ambito: Progettazione del rivestimento Fornitura dei materiali refrattari Montaggio del rivestimento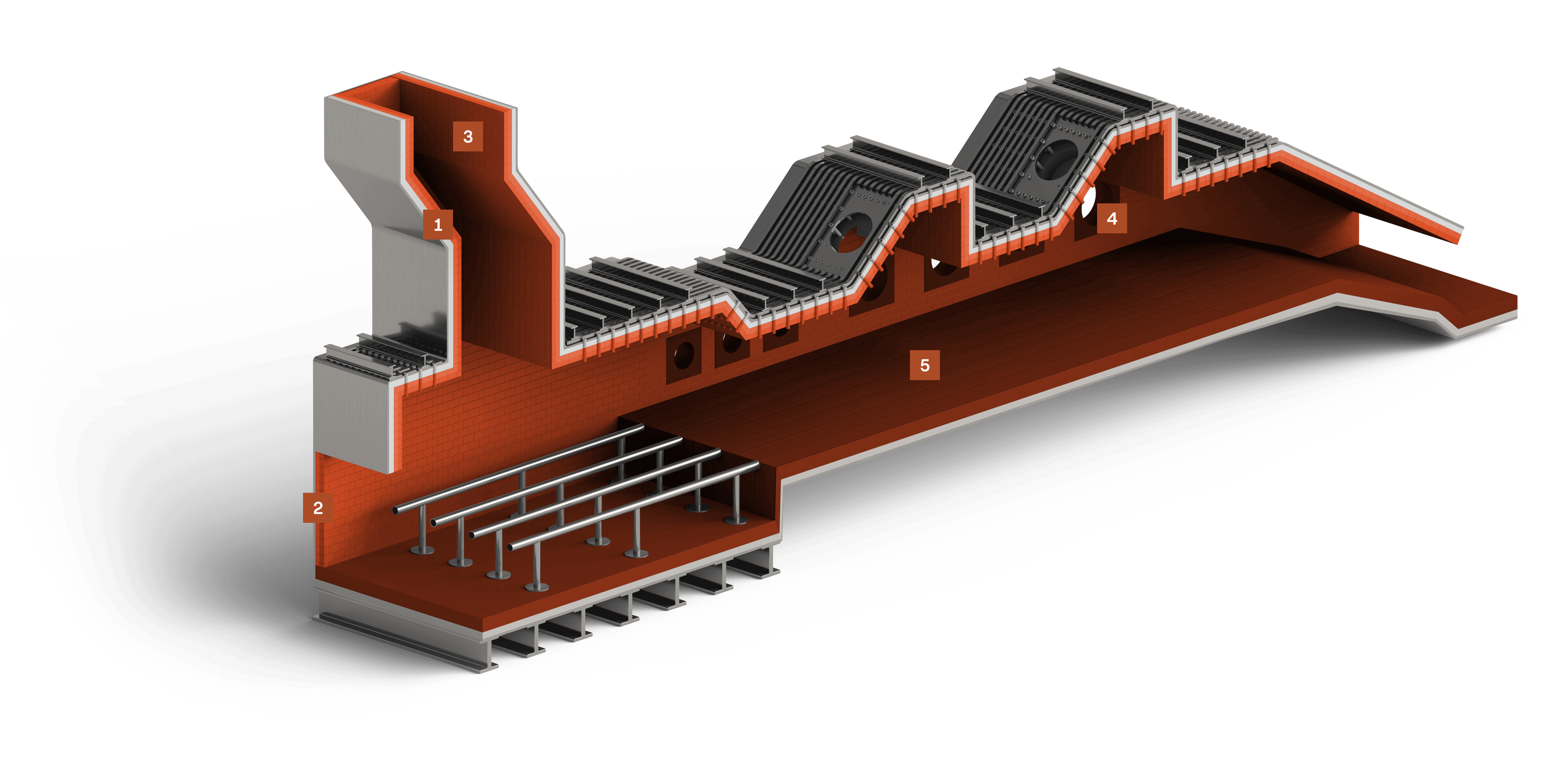
Lo strato ceramico protettivo è realizzato con prodotti ISOLUX isolanti, mattoni chamotte SUPERTON e mattoni ad alto contenuto di allumina ANDALUX. La combinazione di questi materiali permette di mantenere condizioni stabili di lavoro, ridurre le dispersioni termiche e ottimizzare il processo di riscaldamento del metallo, migliorando le prestazioni e riducendo i costi operativi.
Deve offrire eccezionale resistenza all’abrasione, all’ossidazione e agli shock termici, in particolare nelle zone soggette a forti gradienti termici. Si impiegano principalmente mattoni andalusitici ad alto contenuto di allumina (ANDALUX). Per ampie superfici murarie, i prefabbricati in calcestruzzo MULCAST rappresentano una soluzione ideale, grazie alla loro struttura omogenea e resistenza agli agenti aggressivi.
La volta del forno a spinta è esposta all'impatto diretto dei gas di combustione caldi e a grandi differenze di temperatura che si verificano durante i cicli operativi. In tali condizioni, è necessario utilizzare mattoni alluminosilicati con un contenuto di ossido di alluminio (Al₂O₃) compreso tra il 60% e l'80%. In alternativa, per le superfici difficili da rivestire o per formare strati più spessi della volta, si possono utilizzare calcestruzzi refrattari.
I bruciatori sono sottoposti a condizioni termiche e chimiche estreme. PCO Żarów fornisce blocchi per bruciatori in calcestruzzi ad alto tenore di allumina, che grazie alla loro stabilità termica e resistenza meccanica garantiscono la protezione e l’efficienza del processo di riscaldamento.
La suola del forno è l’area più esigente: è a contatto diretto con il metallo caldo e soggetta a gas aggressivi e temperature estreme. I calcestruzzi ad alto contenuto di allumina proposti da PCO garantiscono elevata resistenza termica e meccanica, assicurando la durata e la stabilità strutturale del forno.
Come possiamo aiutarti
Se desideri ricevere una consulenza gratuita o porre una domanda sulla scelta del rivestimento refrattario, lasciaci i tuoi dati – ti richiameremo!
ContattaciQuale materiale protegge meglio la suola del forno contro l’abrasione e la formazione di clinker?
Quale configurazione multistrato riduce lo sfaldamento dello strato interno di mattoni?
Come progettare il rivestimento per massimizzare la resistenza agli urti e alle pressioni meccaniche durante la spinta del carico?
Forno a suole mobili (walking-beam)
Il forno walking-beam è impiegato per il riscaldamento di semilavorati in acciaio di grandi dimensioni e forma regolare, prima della successiva lavorazione plastica in laminatoi. Il materiale avanza grazie a un sistema di travi mobili (“walking beams”), che consente un riscaldamento uniforme ed efficiente. Le temperature operative raggiungono i 1250 °C. Il materiale percorre tre zone principali: preriscaldamento, trasferimento e riscaldamento di bilanciamento. Il rivestimento refrattario deve garantire tenuta ai gas, resistenza agli shock termici e buone proprietà isolanti. Questi requisiti consentono di ridurre le perdite di calore e ottenere un riscaldamento uniforme, condizione essenziale per processi successivi come laminazione o forgiatura.
Ambito: Progettazione del rivestimento Fornitura dei materiali refrattari Montaggio del rivestimento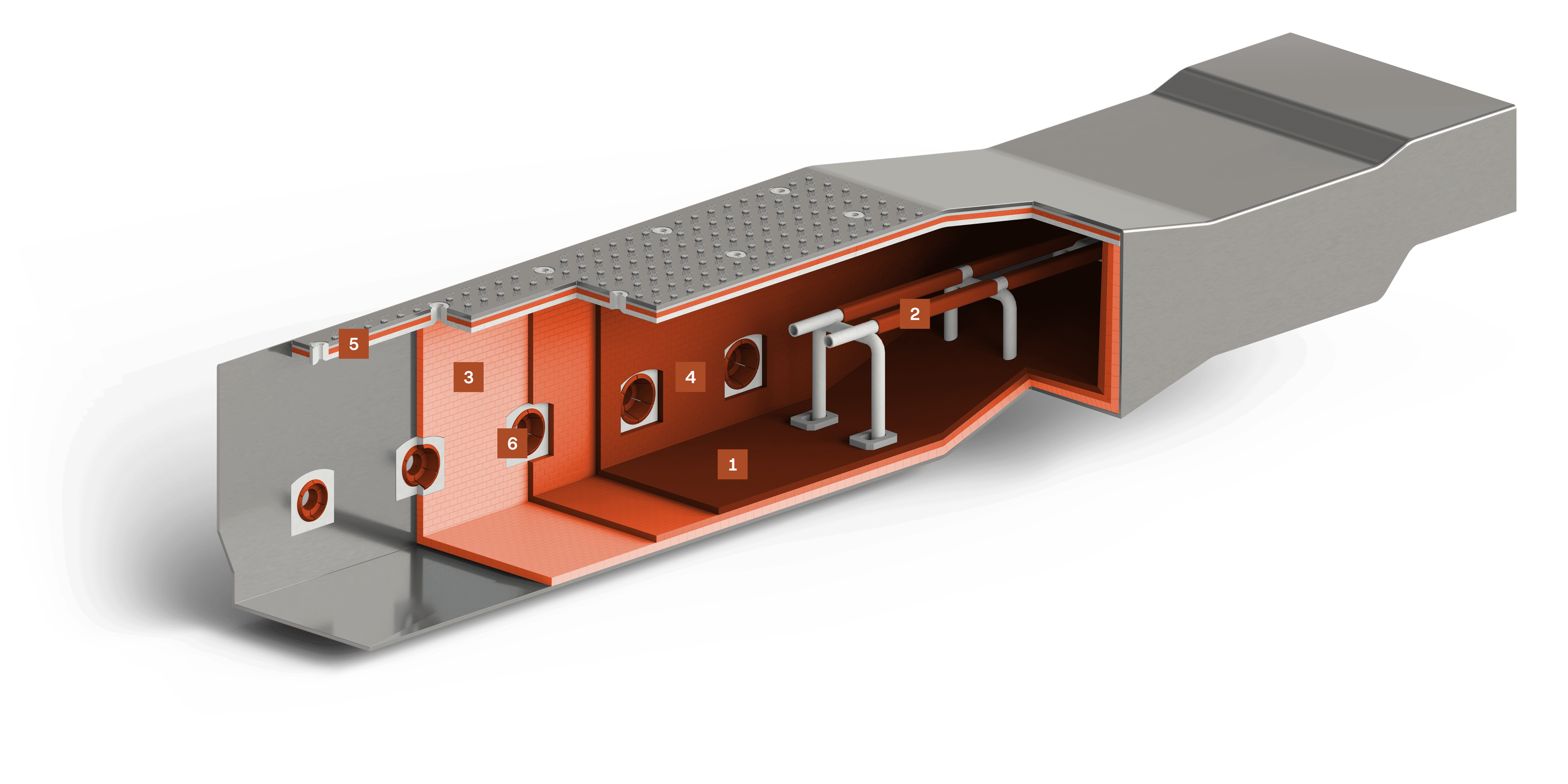
La suola è soggetta a contatto intenso con il metallo caldo, gas aggressivi e temperature estreme. PCO Żarów consiglia calcestruzzi ad alto contenuto di allumina con ottima scorrevolezza, ideali per grandi superfici. In caso di fermo impianto imprevisto, i calcestruzzi “fast dry” sviluppati da PCO consentono un’essiccazione rapida, riducendo i tempi di inattività.
Le travi sono elementi fondamentali per lo scambio termico e il trasporto dei gas. PCO fornisce componenti prefabbricati per condotti verticali e orizzontali, facili da installare o sostituire. Nelle zone complesse come i raccordi a “T”, si impiegano masse da ramming PCO WetRAM, che garantiscono tenuta e stabilità strutturale.
Gli strati protettivi isolano termicamente e proteggono la struttura. Una corretta stratificazione con materiali alluminosilicatici garantisce condizioni operative stabili, ridotte perdite di calore e maggiore efficienza nel riscaldamento del metallo.
Devono essere altamente resistenti ad abrasione, ossidazione e shock termici, specialmente nelle zone a forti gradienti di temperatura. Si usano mattoni andalusitici ad alta allumina (ANDALUX). Per superfici estese, sono ideali i prefabbricati in calcestruzzo, grazie alla struttura omogenea e facilità di posa.
È esposta direttamente ai gas caldi e a forti variazioni termiche. Si impiegano mattoni alluminosilicatici con 60–80% di Al₂O₃, oppure calcestruzzi bauxitici o corindonici, specialmente per geometrie complesse o spessori elevati.
Sottoposti a sollecitazioni termiche e chimiche estreme, richiedono materiali refrattari di elevata resistenza. PCO Żarów propone calcestruzzi ad alto tenore di allumina e a base di corindone che possono essere colati in loco o utilizzati come blocchi per bruciatori prefabbricati. Grazie alla loro struttura compatta e all'alta resistenza agli shock termici, questo calcestruzzo garantisce una stabilità e un'efficienza di funzionamento durature per i bruciatori.
Come possiamo aiutarti
Se desideri ricevere una consulenza gratuita o porre una domanda sulla scelta del rivestimento refrattario, lasciaci i tuoi dati – ti richiameremo!
ContattaciQuale materiale ceramico protegge meglio le travi mobili dai residui che cadono dai bramme riscaldate?
Quale configurazione del rivestimento resiste meglio agli shock termici da introduzione di carico freddo?
Quale materiale minimizza la frantumazione del rivestimento ai bordi delle travi e nelle zone con ancoraggi?
Forno a carrello mobile (bogie hearth furnace)
Il forno a carrello mobile, utilizzato principalmente in fonderie e presse, è destinato al trattamento termico di getti, rilassamento delle tensioni e ricottura di semilavorati e prodotti finiti. A seconda del tipo di carico e degli obiettivi del processo, le temperature operative variano da circa 600 a 1350 °C. Il rivestimento refrattario è realizzato interamente con materiali alluminosilicatici e moduli in fibra ceramica, garantendo stabilità termica e resistenza in condizioni operative estreme. PCO Żarów fornisce soluzioni complete per pareti e volta del forno, nonché diversi tipi di rivestimento per il carrello – da prefabbricati colati a muratura tradizionale.
Ambito: Progettazione del rivestimento Fornitura dei materiali refrattari Montaggio del rivestimento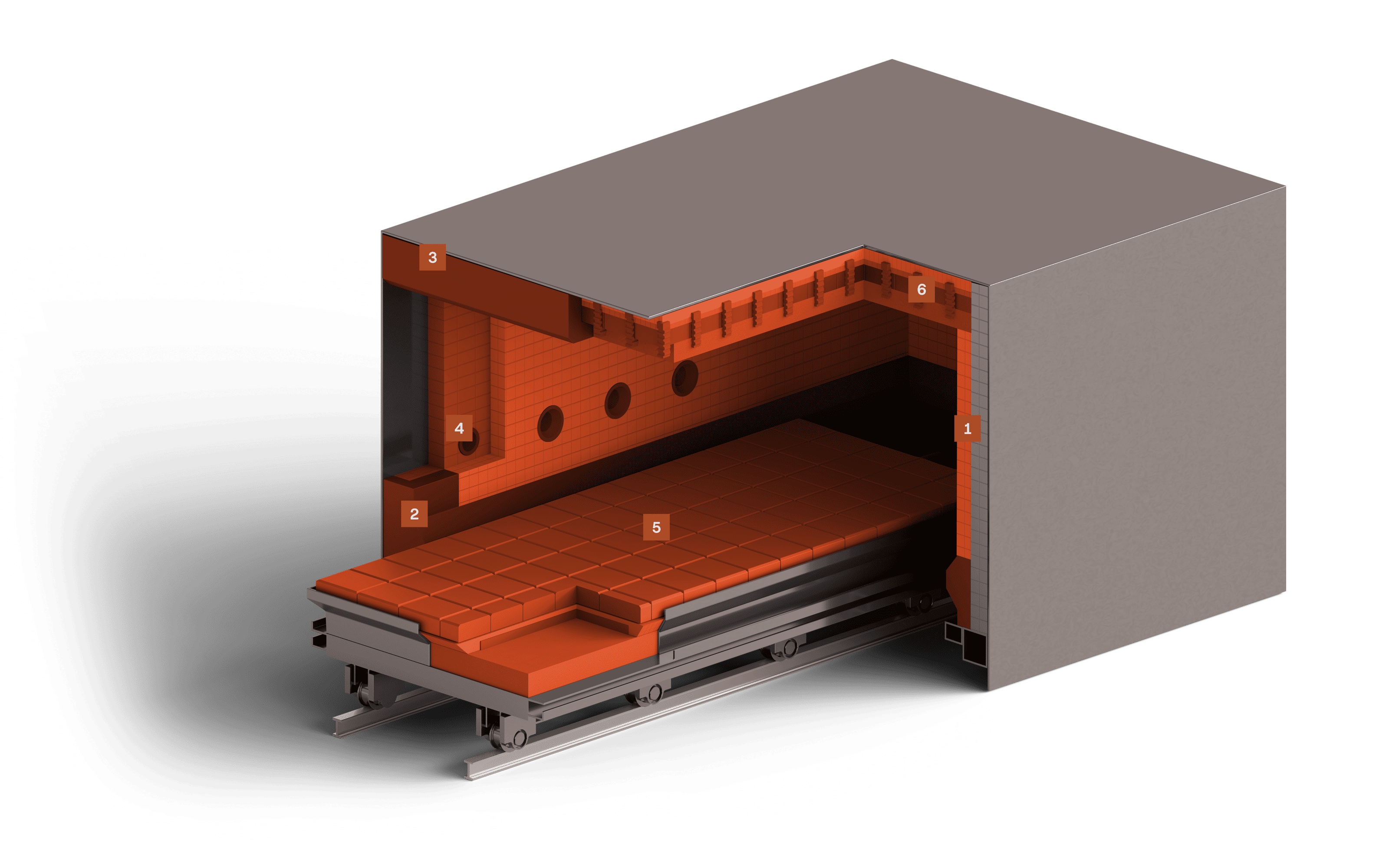
Il rivestimento delle pareti è esposto principalmente a shock termici dovuti alle variazioni di temperatura durante l’apertura del forno. Si utilizza un sistema multistrato in cui lo strato di lavoro è composto da mattoni isolanti. A causa delle temperature moderate (450–1250 °C), la funzione principale delle pareti è l’isolamento termico, non essendo soggette a carichi meccanici intensi.
Situato all’altezza del carrello, il zoccolo delle pareti è soggetto sia a shock termici che a urti meccanici dovuti al movimento del carrello. Richiede materiali ad alta resistenza alla compressione, come calcestruzzi densi o mattoni refrattari compatti. Anche qui si applica una stratificazione multistrato con retrostanti moduli isolanti in fibra.
La porta del forno è realizzata con materiali simili a quelli del zoccolo. In questo caso si usa un calcestruzzo refrattario denso in strato singolo, senza strato isolante secondario.
I bruciatori sono le parti più esposte agli shock termici, operando spesso oltre i 1300 °C. Si impiegano prefabbricati refrattari in calcestruzzo pesante ad alta allumina, che offrono durata e stabilità a lungo termine.
Il carrello è soggetto ai maggiori stress termici, poiché viene ciclicamente raffreddato uscendo dal forno. In molti impianti il ciclo si ripete più volte all’ora. Il rivestimento deve avere alta resistenza meccanica e agli urti. Inoltre, la presenza di ossidi metallici (“zendra”) che si insinuano nelle fughe può causare rotture. Il rivestimento è multilivello e può essere realizzato con prefabbricati o mattoni refrattari compatti nello strato di lavoro.
Esposta a shock termici e alte temperature prolungate. A seconda della progettazione, può essere rivestita con moduli in fibra ceramica per carichi leggeri o con elementi prefabbricati in calcestruzzo refrattario pesante combinati con materiali isolanti. Il fissaggio è garantito da ancoraggi ceramici.
Come possiamo aiutarti
Se desideri ricevere una consulenza gratuita o porre una domanda sulla scelta del rivestimento refrattario, lasciaci i tuoi dati – ti richiameremo!
ContattaciQuale materiale usare su porta e zoccolo per resistere alle sollecitazioni meccaniche del movimento del carrello?
Come progettare la stratificazione e i giunti di dilatazione del carrello per mantenerne l’integrità nel tempo?
Quale materiale scegliere per pareti e volta per combinare resistenza meccanica e resistenza agli shock termici ciclici?
Perché PCO?
Servizio di installazione e fornitura di refrattari: gestione del progetto più semplice e un unico garante della qualità
Precisione dimensionale costante, indipendentemente dalla quantità ordinata
Supporto da parte di progettisti e specialisti dei materiali: ti aiuteremo a selezionare il materiale giusto e garantiremo la supervisione dell'installazione
Prodotti e servizi selezionati
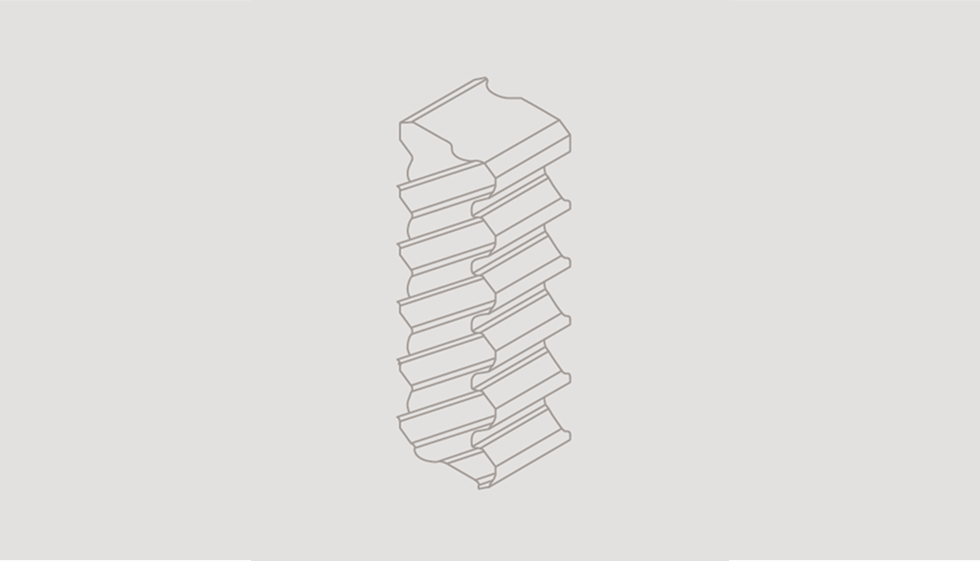
Ancoraggi ceramici
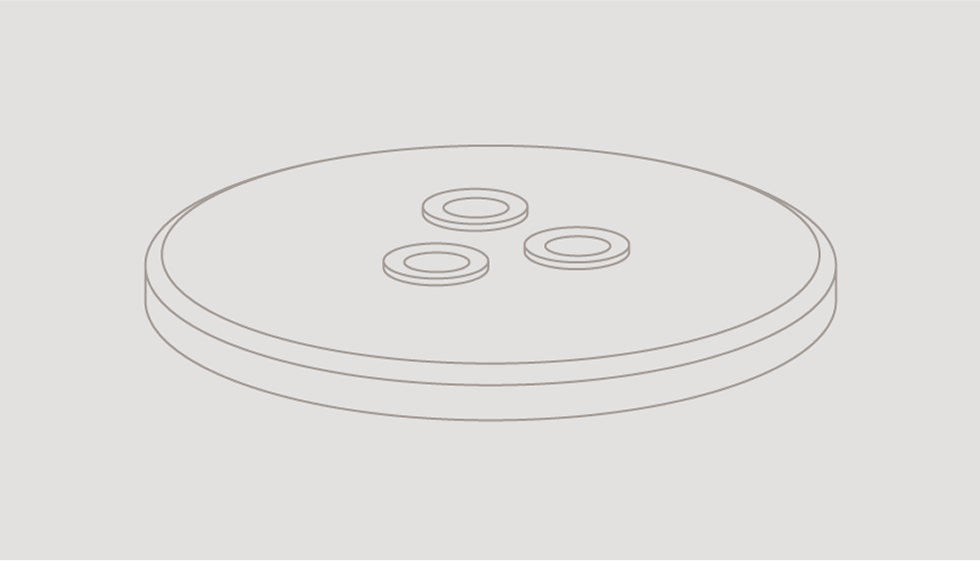
Volta colata per forno EAF
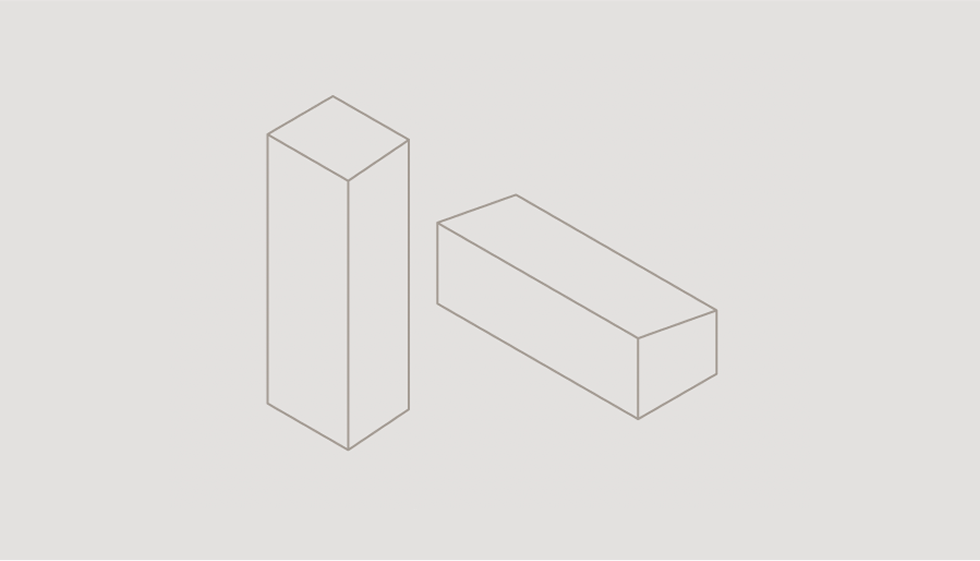
ANDALUX A60Hc-Un (non cotto)
Contattaci
Si prega di selezionare l'opzione che descrive meglio l'argomento che si desidera discutere con noi. Questo ci aiuterà ad indirizzare la tua richiesta alla persona giusta presso PCO.